Hi,
So i had to move house and i used to do some welding there using a BOC 250r (had the 15amp plug) This is Australia btw.
IT was a good machine, and i want to buy something similar, where i have moved to, but i dont have 15amp outlet.
From my understanding all domestic wiring although called 10amp can use 15 amp.
I was considering this machine:
https://www.ewelders.com.au/uni-mig-mig ... -inverter/
http://unimig.com.au/product/unimig-250 ... a-compact/
I hear Unimig is pretty good.. and in melbourne where i am they have warranty and repair.
Is this a decent welder? any other suggestions?
Wondering if i will see much diffrence between a 250 on 10amp 240v Vs the old BOC 250R which had the 15 amp plug... i think it was stil single phase as well.. cause it only had the 3 pins..
General welding questions that dont fit in TIG, MIG, Stick, or Certification etc.
I just made a 15 amp to 10 amp lead and run with that, no problem or difference i could tell from my last house with a dedicated 15amp plug. Uni mig are now Jasic units i believe? Iv got a little 180 uni mig......just shit itself.......but up until now has been awesome. Most units you’ll find are now Chinese manufactured so warranty and local support are the keys.
Esseti AC/DC 200
Uni mig mini mig 180
Rossi ct 416 plasma
Uni mig mini mig 180
Rossi ct 416 plasma
yes and no.Stato wrote:Hi,
So i had to move house and i used to do some welding there using a BOC 250r (had the 15amp plug) This is Australia btw.
IT was a good machine, and i want to buy something similar, where i have moved to, but i dont have 15amp outlet.
From my understanding all domestic wiring although called 10amp can use 15 amp.
i'm not 100% on your house wiring. across the ditch here we run similar regs.
big thing is distance the outlet is from the fuse box. if your close like a meter or so, the wire won't be much of a problem.
but 10m is a big issue. its not just resistance of the wire (which cause volt drop) but also your outside temps. the cables being heated up by the sun adds to the problem. hot cables that are heated up even more by welding can melt.
also the circuit will have a 16 or 17 amp breaker on it. thats to protect the wiring, do not increase it. i think a 250 amp welder will pop the breaker pretty quick.
so, do you really need a 250 amp welder? that a big welder. family have a boc 250 and think its a 25 amp breaker. thats used in commercial use on a farm workshop.
a simple thing is to get a smaller welder. typical 10amp supply welder outputs 140 amp, can got to 160 amp with PFC.
plenty of 180-200 amp welders around for a 15 amp supply.
keep in mind even my 180 amp machine can draw max of 30 odd amps. i run a 20 amp breaker and 15 amp outlet thats less than a meter from the fuse box.
wiring, run a dedicated 15 amp line. or run a 32 amp line to a sub main, then run your outlets off that.
any cabling in walls and ceiling you really want over sized due to the heat build up.
tweak it until it breaks
do not ever do that.Darrin wrote:I just made a 15 amp to 10 amp lead and run with that,....
the problem is the contacts in the 10 outlets are a bit smaller especially on the cheap outlets.
all that happens is they heat up, metal deforms a bit then starts arcing. then one day you will be welding and it will catch on fire and burn up inside the wall and you will never even notice until its way to late.
houses go up in flames every year from that. i've seen way to many melted sockets when i was doing electrical work.
tweak it until it breaks
Bill Beauregard
- Bill Beauregard
-
Weldmonger
-
Posts:
-
Joined:Thu Jan 24, 2013 9:32 pm
-
Location:Green Mountains of Vermont
I've never been down under. I can promise that physics are the same there, and here. A welder needs a dedicated circuit. A dedicated circuit goes without interruption from breaker panel to welder. Installers putting a circuit in place for lighting, or code minimum are allowed to take shortcuts. A welder circuit doesn't do well with shortcuts. Any weak connections will heat. You may ruin your welder, or start a fire in a different room. Have a new dedicated circuit installed for your welder.
240 volt for everything single phase. 10 amp standard house hold socket.Franz© wrote:Aren't you guys clinging to the bottom of the planet running 220 volt household lights and appliances?
tweak it until it breaks
Bill Beauregard
- Bill Beauregard
-
Weldmonger
-
Posts:
-
Joined:Thu Jan 24, 2013 9:32 pm
-
Location:Green Mountains of Vermont
May I assume a standard wall lamp still has two wires, therefore is single phase. Here, some residential structures are multi family, they have three phase, but no three phase loads. It is just a way to bring 1.73 times as much power without big services. Is your welder three phase?
Here we have 15 amp circuits on #14 wire. Some electricians mix lighting circuits with receptacle circuits, and everything is #14. I separate lighting from receptacle circuits. I can't know what will be plugged in so every outlet is powered with #12, and capable of 20 amps. Each connection is capable of failure, and overheating. We make each connection able to carry the full load the breaker can supply. Very few electricians take this trouble.
The greatest hazard is "back wired devices". Here they are legal only for #14 wire, but are commonly used by profit minded contractors even with #12. They are notorious for fire. Typically they work fine for years in circuits used for only basic household loads. When somebody plugs in a heavier load, something is likely to melt.
Here we have 15 amp circuits on #14 wire. Some electricians mix lighting circuits with receptacle circuits, and everything is #14. I separate lighting from receptacle circuits. I can't know what will be plugged in so every outlet is powered with #12, and capable of 20 amps. Each connection is capable of failure, and overheating. We make each connection able to carry the full load the breaker can supply. Very few electricians take this trouble.
The greatest hazard is "back wired devices". Here they are legal only for #14 wire, but are commonly used by profit minded contractors even with #12. They are notorious for fire. Typically they work fine for years in circuits used for only basic household loads. When somebody plugs in a heavier load, something is likely to melt.
10 amps of 240 volts will do one hell of a lot of welding, as long as you're working the low end of the machine's ability.tweake wrote:240 volt for everything single phase. 10 amp standard house hold socket.Franz© wrote:Aren't you guys clinging to the bottom of the planet running 220 volt household lights and appliances?
I've put an Amprobe on my Miller MM-200 and quite a few others, and running at the top of the low range it pulls 17 amps.
Give it a try and see what your results are.
not sure with aussie but we can have a mix of phases depending on local aera.Bill Beauregard wrote:May I assume a standard wall lamp still has two wires, therefore is single phase. Here, some residential structures are multi family, they have three phase, but no three phase loads. It is just a way to bring 1.73 times as much power without big services. Is your welder three phase?
Here we have 15 amp circuits on #14 wire. Some electricians mix lighting circuits with receptacle circuits, and everything is #14. I separate lighting from receptacle circuits. I can't know what will be plugged in so every outlet is powered with #12, and capable of 20 amps. Each connection is capable of failure, and overheating. We make each connection able to carry the full load the breaker can supply. Very few electricians take this trouble.
The greatest hazard is "back wired devices". Here they are legal only for #14 wire, but are commonly used by profit minded contractors even with #12. They are notorious for fire. Typically they work fine for years in circuits used for only basic household loads. When somebody plugs in a heavier load, something is likely to melt.
most places are single phase but some towns are all 3 phase. some places can have two phase. its just down to how local power lines co does the balancing of the power on the phases.
tho inside the house its generally all wired with single phase outlets. those lucky enough with three phase you might wire up a 3 phase outlet in the garage.
typically lights and power sockets are wired with different sized wires and your not allow to use light circuits for power outlets. this all gets inspected and approved etc.
you can daisy chain a lot of outlets together but it has one breaker. dosn't make to much sense to run to many outlets otherwise they trip breakers all the time. also now we have RCD's fitted.
not sure what you mean by "back wired devices" .
the breaker is sized for the cable, so it doesn't matter what load you place on the cable the breaker will trip before the wire heats up to much. you have certain sized cables for certain circuits with matching sized breakers.
used to be a problem years ago when people would use larger sized fuse wire but not so much these days as most breakers are not easily removable, so they can't fit bigger ones without pulling out the panel.
we do not have push in wiring. thats just asking for trouble.
tweak it until it breaks
yes, 10 amp circuit will give you a 140 amp welder which is perfectly fine for a lot of work. (push that to 160 amps with PFC)Franz© wrote:10 amps of 240 volts will do one hell of a lot of welding, as long as you're working the low end of the machine's ability.tweake wrote:240 volt for everything single phase. 10 amp standard house hold socket.Franz© wrote:Aren't you guys clinging to the bottom of the planet running 220 volt household lights and appliances?
I've put an Amprobe on my Miller MM-200 and quite a few others, and running at the top of the low range it pulls 17 amps.
Give it a try and see what your results are.
unfortunately i do not have my old meters any more. have nothing to test amps with these days.
tweak it until it breaks
Bill Beauregard
- Bill Beauregard
-
Weldmonger
-
Posts:
-
Joined:Thu Jan 24, 2013 9:32 pm
-
Location:Green Mountains of Vermont
Code limits for amperage are very conservative. I've never seen a wire burn off mid run unless it was damaged. Connections are quite another matter. When I take other people's work apart I find all sorts of bad connections. Our code books include specific instructions as to how to terminate wire. It's rare to find a connection properly made. I say the hook bent in the wire to wrap around a screw should be J shaped. The plier should grip the very end of the wire, and bring it around 180 degrees. The straight part should be under the screw connection. I want all sides of the screw supported by the wire so it doesn't push the thread sideways in the threaded hole. Tightening to 35 inch pounds is critical, and inspectors want to see the torque screwdriver you used.tweake wrote:not sure with aussie but we can have a mix of phases depending on local aera.Bill Beauregard wrote:May I assume a standard wall lamp still has two wires, therefore is single phase. Here, some residential structures are multi family, they have three phase, but no three phase loads. It is just a way to bring 1.73 times as much power without big services. Is your welder three phase?
Here we have 15 amp circuits on #14 wire. Some electricians mix lighting circuits with receptacle circuits, and everything is #14. I separate lighting from receptacle circuits. I can't know what will be plugged in so every outlet is powered with #12, and capable of 20 amps. Each connection is capable of failure, and overheating. We make each connection able to carry the full load the breaker can supply. Very few electricians take this trouble.
The greatest hazard is "back wired devices". Here they are legal only for #14 wire, but are commonly used by profit minded contractors even with #12. They are notorious for fire. Typically they work fine for years in circuits used for only basic household loads. When somebody plugs in a heavier load, something is likely to melt.
most places are single phase but some towns are all 3 phase. some places can have two phase. its just down to how local
power lines co does the balancing of the power on the phases.
tho inside the house its generally all wired with single phase outlets. those lucky enough with three phase you might wire up a 3 phase outlet in the garage.
typically lights and power sockets are wired with different sized wires and your not allow to use light circuits for power outlets. this all gets inspected and approved etc.
you can daisy chain a lot of outlets together but it has one breaker. dosn't make to much sense to run to many outlets otherwise they trip breakers all the time. also now we have RCD's fitted.
not sure what you mean by "back wired devices" .
the breaker is sized for the cable, so it doesn't matter what load you place on the cable the breaker will trip before the wire heats up to much. you have certain sized cables for certain circuits with matching sized breakers.
used to be a problem years ago when people would use larger sized fuse wire but not so much these days as most breakers are not easily removable, so they can't fit bigger ones without pulling out the panel.
we do not have push in wiring. thats just asking for trouble.
100% of wire overheat failures I have seen are at the point of connection. Wire nuts must be installed in accordance with manufacturer's instructions or they don't qualify as "LISTED". I constantly find wire nuts oversized, loose, exposed to moisture, corroded. There are some I don't believe should be allowed.
Back wired devices are those with holes in the back, a stripped wire is pushed in. A spring grips the wire. Then the wires are folded and the device is shoved into the box. It's like a little crow bar prying on a weak connection. They do overheat.
Willie
ours do not wrap around a screw. they are always sods of things and do not work well with multi strand cables.Bill Beauregard wrote: Our code books include specific instructions as to how to terminate wire. It's rare to find a connection properly made. I say the hook bent in the wire to wrap around a screw should be J shaped.
great if you use crimps. i only see that on low voltage gear (12v etc).
we used hole with a screw through the side.
hopefully i can hot link this pic.
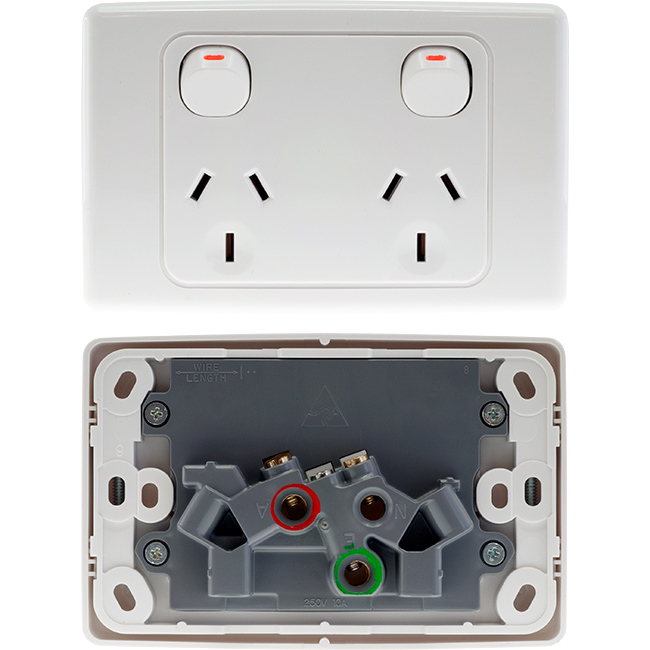
poke the wire in and crank on the screw. for skinny wires you fold it over give a bit more meat for the screw to bite into.
it also makes daisy chaining easy.
one problem i'm told that does arise is connections coming loose over time. not sure of thats just a heat thing or metal thing.
tweak it until it breaks
copper mostly.Franz© wrote:Are you inverted guys using copper or aluminum wire?
there is some aluminum wire around but it do not know what the story is these days. its been 20+ years since i was involved in electrical work.
tweak it until it breaks
buttons are the switches. its single phase 240v.Franz© wrote:Are the buttons above the recepticles switches that operate the receptacle?
What voltage do you get line to ground from both sides of the line?
tweak it until it breaks
can't quite remember, its getting late here.Franz© wrote:what's the voltage red - green or gray -green?
earth and neutral are connected at switchboard so should have 240v red-green and nothing gray-green.
tweak it until it breaks
OK so i think i have made an error.. i thought this was a 250amp with a 10amp plug single phase..(it seemed odd to me because im sure the guy in store said single phase and standard plug ?.. yet we had a 250amp on a 15amp socket..... the machie did not have a plug on it in store so could not tell... obviously he was confused or i was.)tweake wrote:yes, 10 amp circuit will give you a 140 amp welder which is perfectly fine for a lot of work. (push that to 160 amps with PFC)Franz© wrote:10 amps of 240 volts will do one hell of a lot of welding, as long as you're working the low end of the machine's ability.tweake wrote: 240 volt for everything single phase. 10 amp standard house hold socket.
I've put an Amprobe on my Miller MM-200 and quite a few others, and running at the top of the low range it pulls 17 amps.
Give it a try and see what your results are.
unfortunately i do not have my old meters any more. have nothing to test amps with these days.
So i would need a dedicated 15amp outlet to get that welder. (essentially a dedicated outlet back to the powerboard with larger wire)
So i may need to step down to about a 180amp machine... Unimig make this..
https://www.ewelders.com.au/unimig-vipe ... r-package/
To Quote them:
Ever wanted wanted to be able to plug a semi-industrial Powered MIG welder straight into a standard 10amp power point? Here's your answer.
The UniMig Viper MIG 180 is the most powerful MIG welder in Australia legally fitted with a 10amp plug. The Viper MIG has added MMA (Arc) function, uses Jasic's renowned inverter technology and is extremely competitively priced making it ideal for the serious DIY usr or tradesman.
It will probably do the Job TBH, The thickest id be welding is 10mm maybe.. and not alot of it... or long runs.
I was thinking 250amp because the one i used was really good... and i didnt want to risk being disappointed by getting something smaller.. But i think for what i do i will be fine, and it is cheaper to boot.
Any Other suggestions?
Thanks for your input all of you. Cheers.
Buy the 250 and make an adapter cord.
Why is it you inverted people are so confused? You use amps & volts like civilized people, but you can't understand inches. You used to be able to understand inches. The damn limeys invented inches.
Use proper measurments.
Do you realize that damn metric crud forces decent people to grab rulers to understand what you're talking about?
Why is it you inverted people are so confused? You use amps & volts like civilized people, but you can't understand inches. You used to be able to understand inches. The damn limeys invented inches.
Use proper measurments.
Do you realize that damn metric crud forces decent people to grab rulers to understand what you're talking about?
Bill Beauregard
- Bill Beauregard
-
Weldmonger
-
Posts:
-
Joined:Thu Jan 24, 2013 9:32 pm
-
Location:Green Mountains of Vermont
Is it actually the tip of the screw that contacts the wire? I'm not impressedtweake wrote:ours do not wrap around a screw. they are always sods of things and do not work well with multi strand cables.Bill Beauregard wrote: Our code books include specific instructions as to how to terminate wire. It's rare to find a connection properly made. I say the hook bent in the wire to wrap around a screw should be J shaped.
great if you use crimps. i only see that on low voltage gear (12v etc).
we used hole with a screw through the side.
hopefully i can hot link this pic.
poke the wire in and crank on the screw. for skinny wires you fold it over give a bit more meat for the screw to bite into.
it also makes daisy chaining easy.
one problem i'm told that does arise is connections coming loose over time. not sure of thats just a heat thing or metal thing.
Actually I think they tried to make Square D's screw terminal a little better for stranded wire.
The tapered tip supposedly spreads individual strands and increases contact area with the barrel of the connector.
It's still a hell of a lot better than the fake spring loaded SPEEDWIRE crap millions of houses with PVC enclosures here use.
Never ask an electrical inspector why PVC is a good idea for wall boxes and breaker pannels but no good for conduit above a suspended ceiling. They get all glassy eyed and start yelling code.
The tapered tip supposedly spreads individual strands and increases contact area with the barrel of the connector.
It's still a hell of a lot better than the fake spring loaded SPEEDWIRE crap millions of houses with PVC enclosures here use.
Never ask an electrical inspector why PVC is a good idea for wall boxes and breaker pannels but no good for conduit above a suspended ceiling. They get all glassy eyed and start yelling code.
ex framie
- ex framie
-
Ace
-
Posts:
-
Joined:Sun Aug 09, 2015 1:09 am
-
Location:Brisbane QLD Land of oz
I have been looking at upgrading my old wia 150s mig to either a 200 or 250 amp machine.
I have several dedicated 15 amp single phase circuits in my shed.
The issue is I would like a 250 amp unit, however the small print recommendation seems to be a requirement for a 25 to 30 amp circuit for the unit to put out the full 250 amps, (thats why the unit you looked at didnt have a plug fitted in the store) not economically feasable for me to upgrade the feed wire to the shed as its under ground.
So if a 250 amp machine requires 25 to 30 amps to operate to its full potential, you have buckleys chance of getting it out of a 10 amp circuit.
However going back down to a 200 amp machine, it will run to its full capacity on a 15 amp circuit, apparently.
So your idea of a 180 amp machine should work on a 15 amp circuit, 10 amp would limit the output to lower levels and would probably continually trip the breaker when the amps are turned up or you weld for more than a minute.
Cheers
I have several dedicated 15 amp single phase circuits in my shed.
The issue is I would like a 250 amp unit, however the small print recommendation seems to be a requirement for a 25 to 30 amp circuit for the unit to put out the full 250 amps, (thats why the unit you looked at didnt have a plug fitted in the store) not economically feasable for me to upgrade the feed wire to the shed as its under ground.
So if a 250 amp machine requires 25 to 30 amps to operate to its full potential, you have buckleys chance of getting it out of a 10 amp circuit.
However going back down to a 200 amp machine, it will run to its full capacity on a 15 amp circuit, apparently.
So your idea of a 180 amp machine should work on a 15 amp circuit, 10 amp would limit the output to lower levels and would probably continually trip the breaker when the amps are turned up or you weld for more than a minute.
Cheers
Pete
God gave man 2 heads and only enough blood to run 1 at a time. Who said God didn't have a sense of humour.....
God gave man 2 heads and only enough blood to run 1 at a time. Who said God didn't have a sense of humour.....
Bill Beauregard
- Bill Beauregard
-
Weldmonger
-
Posts:
-
Joined:Thu Jan 24, 2013 9:32 pm
-
Location:Green Mountains of Vermont
A wall box serves one purpose; it contains a fire. For many years I resisted, and still used metal boxes. They stand a good chance of containing a fire. Then, I realized that my competitors were undercutting my price by using plastic boxes, twist wire nuts, and lots of #14 wire. I figured out I wasn't making anything safer when I was losing jobs to corner cutting electricians. I have surrendered, I use some plastic boxes, yes I'm ashamed. I use some twist wire nuts, yes I'm ashamed. I haven't surrendered ALL ethics, I won't use back wired devices. Yes, I use a ton of plastic conduit. Fires don't start mid span. Fires start at connections.Franz© wrote:Actually I think they tried to make Square D's screw terminal a little better for stranded wire.
The tapered tip supposedly spreads individual strands and increases contact area with the barrel of the connector.
It's still a hell of a lot better than the fake spring loaded SPEEDWIRE crap millions of houses with PVC enclosures here use.
Never ask an electrical inspector why PVC is a good idea for wall boxes and breaker pannels but no good for conduit above a suspended ceiling. They get all glassy eyed and start yelling code.
Willie
Return to “Welding Forum General Shop Talk”
Jump to
- Introductions & How to Use the Forum
- ↳ Welcome!
- ↳ Member Introductions
- ↳ How to Use the Forum
- ↳ Moderator Applications
- Welding Discussion
- ↳ Metal Cutting
- ↳ Tig Welding - Tig Welding Aluminum - Tig Welding Techniques - Aluminum Tig Welding
- ↳ Mig and Flux Core - gas metal arc welding & flux cored arc welding
- ↳ Stick Welding/Arc Welding - Shielded Metal Arc Welding
- ↳ Welding Forum General Shop Talk
- ↳ Welding Certification - Stick/Arc Welding, Tig Welding, Mig Welding Certification tests - Welding Tests of all kinds
- ↳ Welding Projects - Welding project Ideas - Welding project plans
- ↳ Product Reviews
- ↳ Fuel Gas Heating
- Welding Tips & Tricks
- ↳ Video Discussion
- ↳ Wish List
- Announcements & Feedback
- ↳ Forum News
- ↳ Suggestions, Feedback and Support
- Welding Marketplace
- ↳ Welding Jobs - Industrial Welding Jobs - Pipe Welding Jobs - Tig Welding Jobs
- ↳ Classifieds - Buy, Sell, Trade Used Welding Equipment
- Welding Resources
- ↳ Tradeshows, Seminars and Events
- ↳ The Welding Library
- ↳ Education Opportunities