Was thinking if building a welding table soon.. So what is the thickness of material y'all are using. This will be a compact table just to build maybe a couple off road bumpers and prefab exhaust on. Small light duty stuff around the house
Sent from my DROID RAZR HD using Tapatalk
General welding questions that dont fit in TIG, MIG, Stick, or Certification etc.
- Otto Nobedder
-
Weldmonger
-
Posts:
-
Joined:Thu Jan 06, 2011 11:40 pm
-
Location:Near New Orleans
If you're not going to be hammering on it, 1/4" is plenty.
If you think you may really abuse it in the future, go with 1/2" or better.
Steve S
If you think you may really abuse it in the future, go with 1/2" or better.
Steve S
kermdawg
- kermdawg
-
Weldmonger
-
Posts:
-
Joined:Tue May 25, 2010 8:16 pm
-
Location:All over, mostly southwest USA
Personally I feel less important is the thickness of the top and more important is whats underneath. If you reinforce the hell out of the underneath of the top you don't need nearly as much thickness. I used 1" sch 40 pipe for slats spaced at 6" on center and some 14 guage scrap for the top. I call it the franken table
I beat the crap outta it and the top itself is fine, but I went cheap on the outer frame (1/8"x1"angle) and the frame actually bent. I would definately recommend at least 1/4" for your legs and frame.
But as with anything, it doesn't hurt to go thicker/bigger/wider, as long as you don't have to move the damn thing!
maybe think about some locking casters!
edit-Reread your original post. 1/4" is more than enough for light fab work.

But as with anything, it doesn't hurt to go thicker/bigger/wider, as long as you don't have to move the damn thing!

edit-Reread your original post. 1/4" is more than enough for light fab work.
Signature? Who needs a F***ing signature?
Thanks guys. The previous owner of my house, her grandson left his welding table but the legs are 1/8 angle not sure on the top surface so I was gonna modify it
Sent from my DROID RAZR HD using Tapatalk
Sent from my DROID RAZR HD using Tapatalk
Don't discount wood either. I know many welders will groan at the idea but it's handy for jigging on the fly. Some 2"x2" blocks with screws in them and you have a jig system for everything. When I weld steel on it, I can TIG weld one half of all the welds on the table without messing it up too badly. I just use a piece of tile board from the big box stores as a sacrificial drawing/welding surface. I also have pieces of 2"x2"x1/4" aluminum angle for jig blocks I can use, and a case of 2.5" drywall screws.
This particular table has 2x2 angle iron frame with two layers of 3/4" plywood on it. Anything extra hot, I can tack it on the table, and then hang the larger-hotter welds past the table top and tack braces on the weldments to act as a jig as well. Between that and a crooking stand, I can weld, bend, and tweak out any weld distortion more efficiently and quickly than jigs or clamps. I have been fabricating on this same table for 14 years. The plywood under the tile board is still clean, outside of the zillion screw holes in it by now.
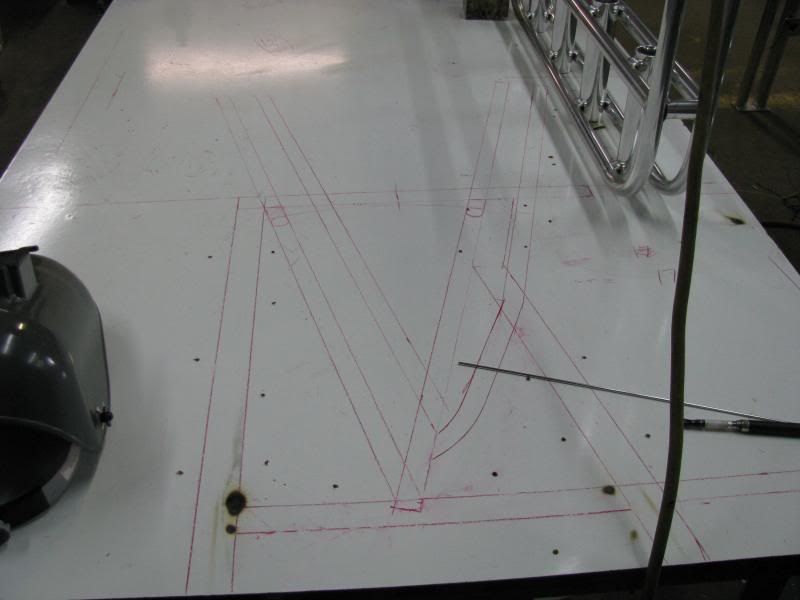
A box of china markers and a bottle of naptha and I can draft and build on this surface for 6 months or more of every day use before treating myself to a new tile board. .
This particular table has 2x2 angle iron frame with two layers of 3/4" plywood on it. Anything extra hot, I can tack it on the table, and then hang the larger-hotter welds past the table top and tack braces on the weldments to act as a jig as well. Between that and a crooking stand, I can weld, bend, and tweak out any weld distortion more efficiently and quickly than jigs or clamps. I have been fabricating on this same table for 14 years. The plywood under the tile board is still clean, outside of the zillion screw holes in it by now.
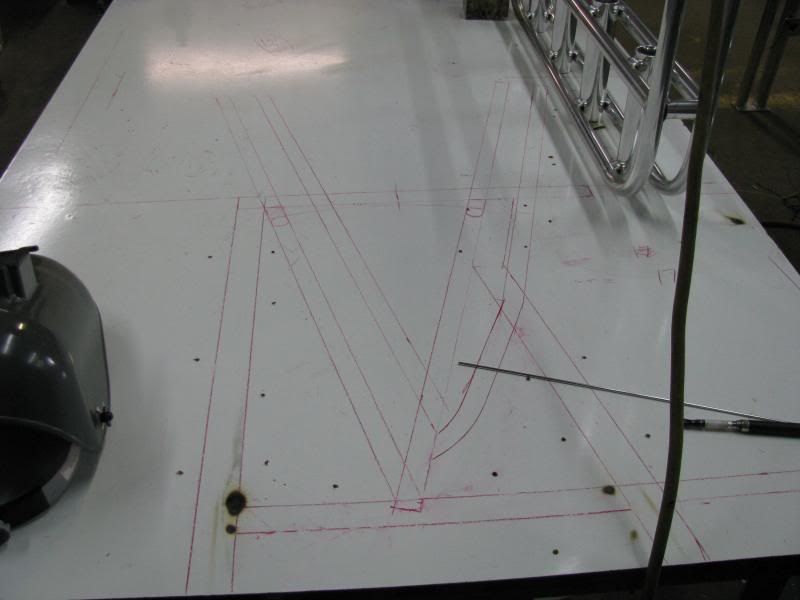
A box of china markers and a bottle of naptha and I can draft and build on this surface for 6 months or more of every day use before treating myself to a new tile board. .
Miller ABP 330, Syncrowave 250, Dynasty 300 DX.
Honorary member of the Fraternity of Faded Tee Shirts.
Honorary member of the Fraternity of Faded Tee Shirts.
nightscale
- nightscale
-
New Member
-
Posts:
-
Joined:Tue Mar 25, 2014 10:21 pm
this is a great idea i think i might do it with my tableTamJeff wrote:Don't discount wood either. I know many welders will groan at the idea but it's handy for jigging on the fly. Some 2"x2" blocks with screws in them and you have a jig system for everything. When I weld steel on it, I can TIG weld one half of all the welds on the table without messing it up too badly. I just use a piece of tile board from the big box stores as a sacrificial drawing/welding surface. I also have pieces of 2"x2"x1/4" aluminum angle for jig blocks I can use, and a case of 2.5" drywall screws.
This particular table has 2x2 angle iron frame with two layers of 3/4" plywood on it. Anything extra hot, I can tack it on the table, and then hang the larger-hotter welds past the table top and tack braces on the weldments to act as a jig as well. Between that and a crooking stand, I can weld, bend, and tweak out any weld distortion more efficiently and quickly than jigs or clamps. I have been fabricating on this same table for 14 years. The plywood under the tile board is still clean, outside of the zillion screw holes in it by now.
A box of china markers and a bottle of naptha and I can draft and build on this surface for 6 months or more of every day use before treating myself to a new tile board. .
cheers
Sent from my SM-N9005 using Tapatalk
I also have a couple 12"x 24" slabs of 1/2" steel plate that I can set on the table if need be, which essentially takes the place of a small steel table on most days. As far as weight, a bottom shelf can hold additional weight. when needed.
I need my table for too many different kinds of materials. My home fab table was essentially a mortise and tenon, scaled down picnic style trestle table, that was actually strong enough to set a v8 small block on.
Very few home fabricators will need an all out welding table, and anything larger than smallish tables will allow, will need to be constructed on itself anyway, such as home built trailers and the likes.
I need my table for too many different kinds of materials. My home fab table was essentially a mortise and tenon, scaled down picnic style trestle table, that was actually strong enough to set a v8 small block on.
Very few home fabricators will need an all out welding table, and anything larger than smallish tables will allow, will need to be constructed on itself anyway, such as home built trailers and the likes.
Miller ABP 330, Syncrowave 250, Dynasty 300 DX.
Honorary member of the Fraternity of Faded Tee Shirts.
Honorary member of the Fraternity of Faded Tee Shirts.
Return to “Welding Forum General Shop Talk”
Jump to
- Introductions & How to Use the Forum
- ↳ Welcome!
- ↳ Member Introductions
- ↳ How to Use the Forum
- ↳ Moderator Applications
- Welding Discussion
- ↳ Metal Cutting
- ↳ Tig Welding - Tig Welding Aluminum - Tig Welding Techniques - Aluminum Tig Welding
- ↳ Mig and Flux Core - gas metal arc welding & flux cored arc welding
- ↳ Stick Welding/Arc Welding - Shielded Metal Arc Welding
- ↳ Welding Forum General Shop Talk
- ↳ Welding Certification - Stick/Arc Welding, Tig Welding, Mig Welding Certification tests - Welding Tests of all kinds
- ↳ Welding Projects - Welding project Ideas - Welding project plans
- ↳ Product Reviews
- ↳ Fuel Gas Heating
- Welding Tips & Tricks
- ↳ Video Discussion
- ↳ Wish List
- Announcements & Feedback
- ↳ Forum News
- ↳ Suggestions, Feedback and Support
- Welding Marketplace
- ↳ Welding Jobs - Industrial Welding Jobs - Pipe Welding Jobs - Tig Welding Jobs
- ↳ Classifieds - Buy, Sell, Trade Used Welding Equipment
- Welding Resources
- ↳ Tradeshows, Seminars and Events
- ↳ The Welding Library
- ↳ Education Opportunities