I'm wondering what I can do to fix the puddle wander on 4130 when it starts to get hot. I try to back off the heat and it still wanders. I have tried starting to manually pulse and it helps, but can't seem to recover fully. Any tricks...?
6G
4130 / .050 wall / 1" dia.
Chief
Welding Certification test Q&A and tips and tricks
- LtBadd
-
Weldmonger
-
Posts:
-
Joined:Sun Apr 12, 2015 4:00 pm
-
Location:Clearwater FL
-
Contact:
Chief, welcome to the forum.
Welding 6G 4130 / .050 wall / 1" dia. tube is going to get heat saturated very quick causing even more puddle wandering. When you add filler that will help a little, but you also need to move as fast as possible while still getting a good weld.
Can you post a pic of the weld you're doing?
Welding 6G 4130 / .050 wall / 1" dia. tube is going to get heat saturated very quick causing even more puddle wandering. When you add filler that will help a little, but you also need to move as fast as possible while still getting a good weld.
Can you post a pic of the weld you're doing?
Richard
Website
Website
Wouldn’t welding downhill help somewhat? Obviously you can’t weld entirely downhill, but starting at 12 and coming down to 6 is how I approach thin walled tubing in a 6G position.LtBadd wrote:Chief, welcome to the forum.
Welding 6G 4130 / .050 wall / 1" dia. tube is going to get heat saturated very quick causing even more puddle wandering. When you add filler that will help a little, but you also need to move as fast as possible while still getting a good weld.
Can you post a pic of the weld you're doing?
I will try welding faster on Tuesday. I can post pics Tuesday as well. I have been starting at the 11 o’clock and welding downhill to 6 o’clock passing through 1,2,3... ect. It starts to wander around 5 o’clock all the way through back to 11.
Don't tell everyone how good you are
Show them
Show them
Thanks for the tips, I will try these today and let you know the outcome. Here are some pictures of my current setup and last weld.
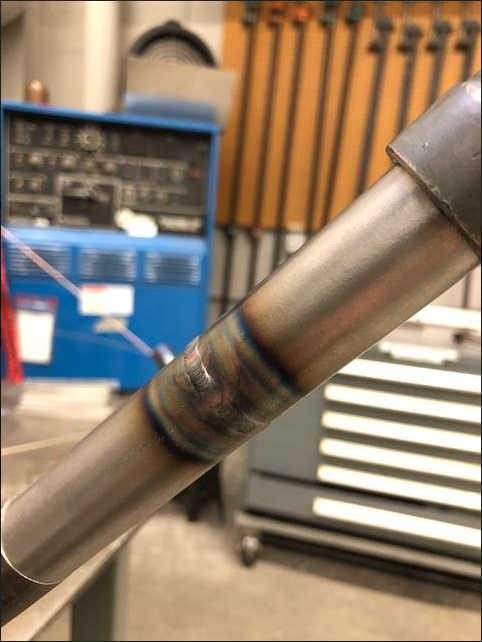
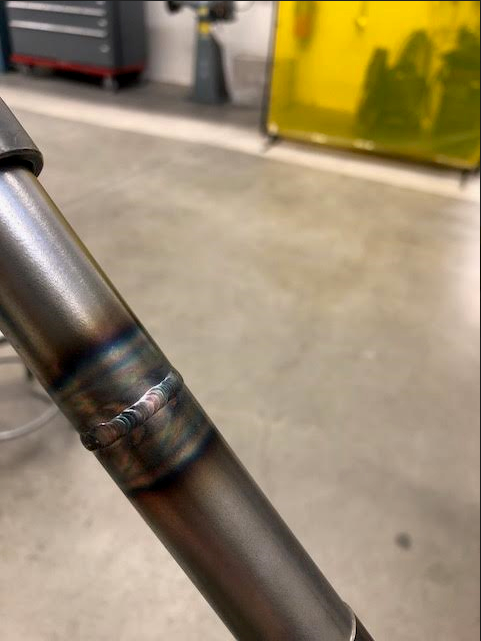
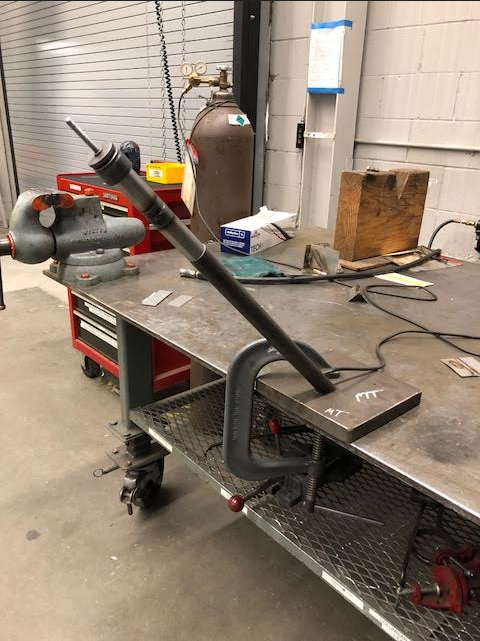
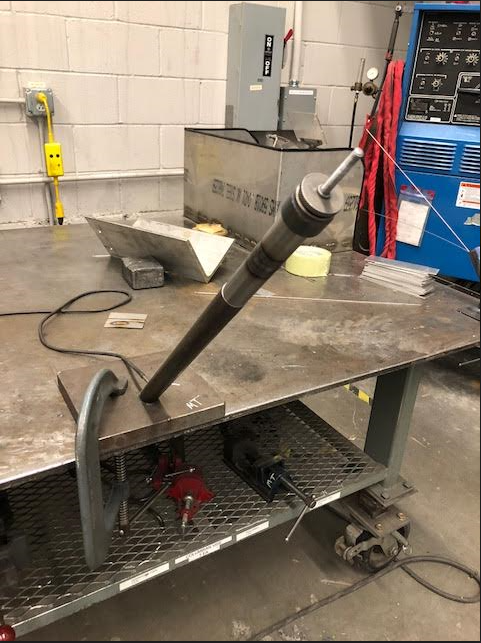
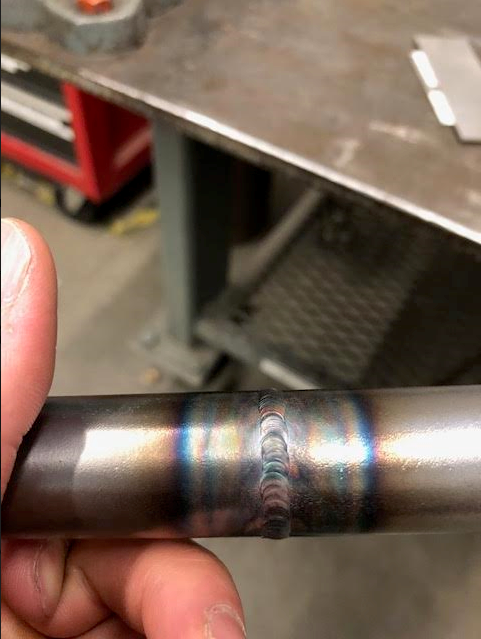
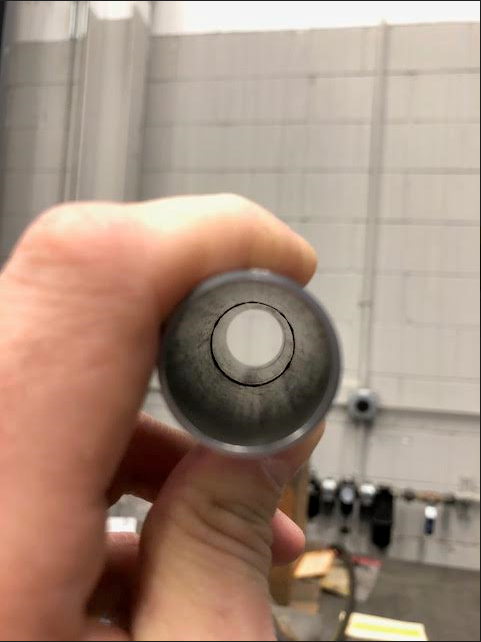
https://lensdump.com/a/welding-cert.8ydZa
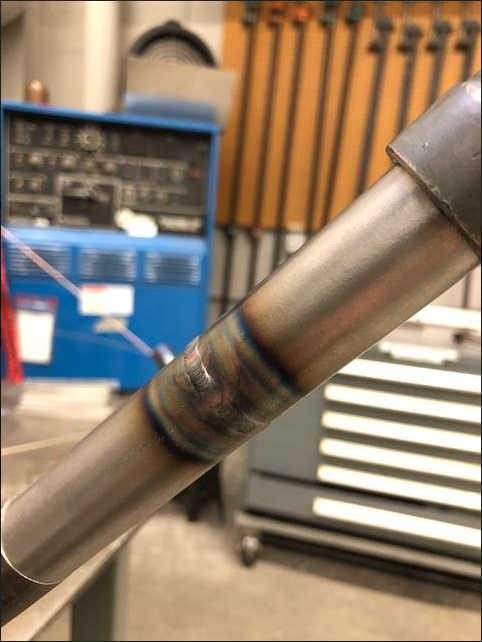
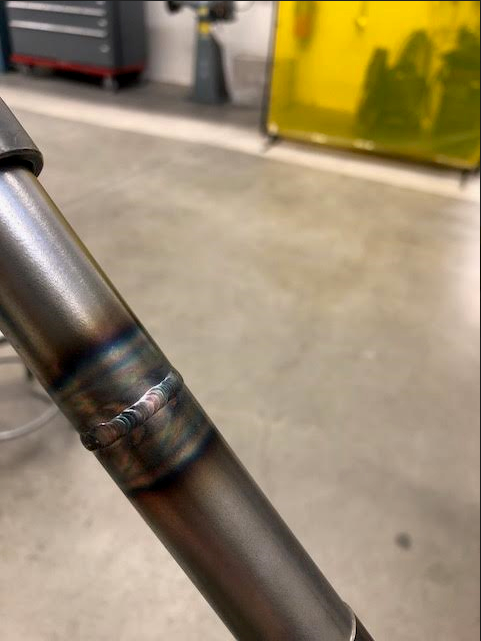
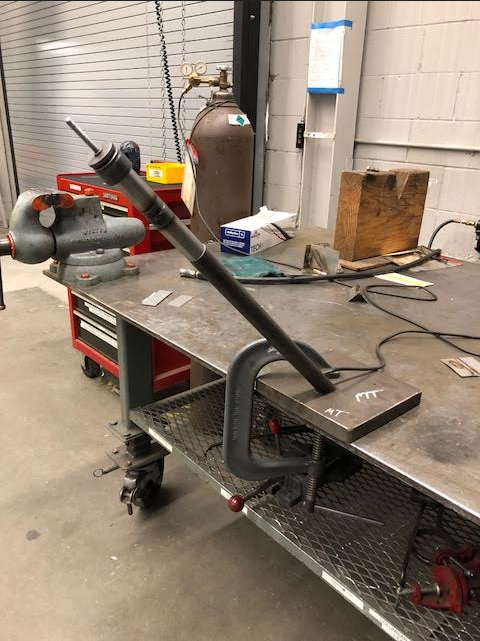
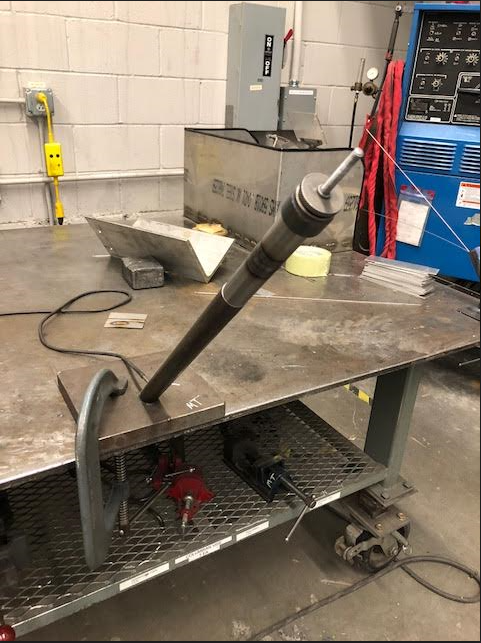
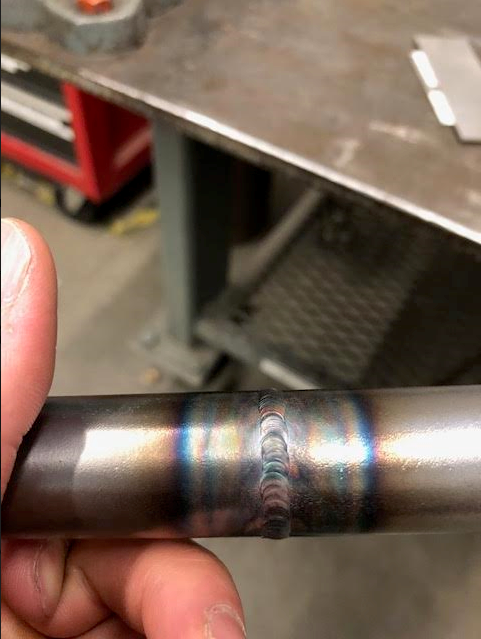
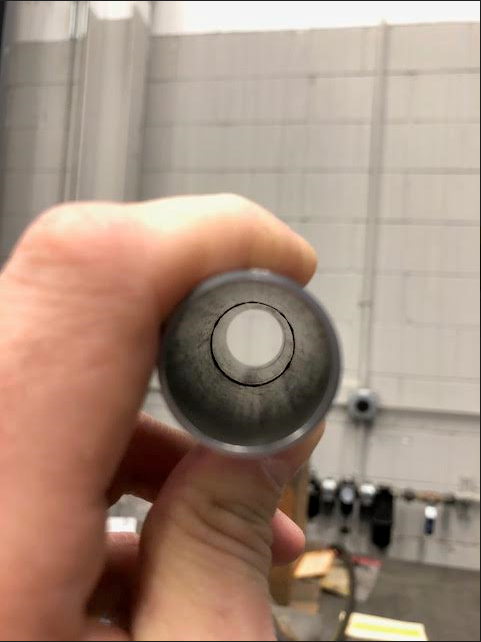
https://lensdump.com/a/welding-cert.8ydZa
Don't tell everyone how good you are
Show them
Show them
Welding from 11 back down helped a little at first, but as soon as i got about half way down it started again. These tubes are so small, I can't find a way to stop or slow the heat saturation. arggghhh... getting better though.
Don't tell everyone how good you are
Show them
Show them
If I may be so bold... it looks like you’re using a fairly thick filler wire? Thicker filler requires more heat, thus saturating the tube. Can you drop down in size? Maybe some 0.45 wire? That should require less amps. Of course, you could always allow the part to cool a bit before you do the other side...
The only chromoly filler we have is 1/16" ER70-S2. I wish I could order .045 but shop sup says no, just figure it out. I will try letting it cool between sections. Patience is a virtue I wish I had more of 

Don't tell everyone how good you are
Show them
Show them
The only chromoly filler we have is 1/16" ER70-S2. I wish I could order .045 but shop sup says no, just figure it out. I will try letting it cool between sections. Patience is a virtue I wish I had more of 

Don't tell everyone how good you are
Show them
Show them
70s2 isn’t actually chrome moly filler. It may work but it won’t be a reliable joint.
http://www.harrisproductsgroup.com/~/me ... MOSpec.pdf
There are fillers designed for your application.
http://www.harrisproductsgroup.com/~/me ... MOSpec.pdf
There are fillers designed for your application.
I have more questions than answers
Josh
Josh
I’m trying to get a hold of some ER80S-D2 or some MIL-R-5632, that stuff is expensive though. The only other rod I have is B50T41A (Turbaloy 1212) which I don’t know anything about
Don't tell everyone how good you are
Show them
Show them
If you want to maintain the strength and corrosion properties of chromemoly, you need the proper filler. You can’t just substitute another filler. When your welding you are literally mixing metals. Not using the proper filler can actually make the joint weake. This is a very common issue with high chrome metals. You also need to monitor interpass temps and use the proper preheat. Granted you can stick metal togeather even with the inproper filler but you can’t rely on the finished product. What is the reason your working with chrome moly tube?
I have more questions than answers
Josh
Josh
- LtBadd
-
Weldmonger
-
Posts:
-
Joined:Sun Apr 12, 2015 4:00 pm
-
Location:Clearwater FL
-
Contact:
Josh, perhaps you are speaking in general about 4130, I had the understanding that 1/8" and thinner material doesn't require preheat.Poland308 wrote: You also need to monitor interpass temps and use the proper preheat. Granted you can stick metal togeather even with the inproper filler but you can’t rely on the finished product. What is the reason your working with chrome moly tube?
OP. If your sup won't let you buy .045" wire, which should be less then $5 a pound then...

Maybe while the weld is cooling, you can prep more practice coupons?
Richard
Website
Website
Im a machinist / welder in the military. I am required to maintain my 6g certs in 4130, 347, 6061, and 718. I have passed my stainless 347 already. I’m surprised you say 70s2 isn’t a proper filler. From what I’ve read and seen 70s2 is very common for welding 4130. Our 6g cert requires no preheat and 70s-2, 80s-d2 or mil-r-5632 for filler.
Don't tell everyone how good you are
Show them
Show them
70S-2 is the most commmon wire CroMo is welded with. 80SD-2 is next best choice, 70S-6 the third. You don’t need preheat on thin material, really only beyond 1/2” which also wants heat treat afterwards.
Probably 95% of all bike frames in CroMo are welded with 70S-2, and every motorcycle frame is too. There is a small movement in the bike frame world leaning towards 80SD-2 for its better ductility, but that industry changes s-l-o-w-l-y.
I’ve welded with both, and I can tell you I have not been able to discern one iota of difference in medieval DTs.
Probably 95% of all bike frames in CroMo are welded with 70S-2, and every motorcycle frame is too. There is a small movement in the bike frame world leaning towards 80SD-2 for its better ductility, but that industry changes s-l-o-w-l-y.
I’ve welded with both, and I can tell you I have not been able to discern one iota of difference in medieval DTs.
Thanks CJ. I will just continue using the 70s2. I don’t know why Poland is saying it’s not a chromoly filler... I’m still chugging along. I’m the only guy in the shop who loves to weld but I have the least experience, so I’m trying to learn all I can.
Don't tell everyone how good you are
Show them
Show them
It depends on the intended purpose of the pipe. There is a reason why they make filler specific to chrom moly pipe. If you have a wps that says it’s ok for your intended use then your fine to use 70s2. Some pipe does specify that the minimum preheat is 50F. So sometimes your ok or not. Again depending on WPS if your qualifying for a test. I noticed his examples are test parts in a purge jig. So I figured he might be trying to qualify for a cert. if so then not just any filler will do. It has to match not just metal but also size of filler, amp range, preheat and interpass temps.
I have more questions than answers
Josh
Josh
I bought a pound of 0.045 ER80 and it was $45. Fortunately, it only takes 3 pieces to do an entire bike frame... The filler is far and above more expensive than the tubing for Pete's Sake!chief775 wrote:BTW that mil-r filler costs over $400 a 10lb box haha
I’d like to know where and when you bought that, and if it was indeed ER80 and was 0.045 wire. Obviously different fillers cost differently, and it seems that the thinner the wire, the more it costs sometimes. And bulk buys reduce the cost as well.Oscar wrote:$45 for ONE pound of 0.045" ER80S-D2? Were you held at gun-point and forced to buy from a certain supplier?I paid $6/lb when I bought 10lbs of it.
Yep, he’s right. I did a new search after that post and found it widely available for under $6/#. Fcuk me. Great thing about this forum, helps you get your head out of your butt occasionally.LtBadd wrote:Last year I bought 1 lb from my LWS at $5.32, this was 1/16" but still .045" couldn't be much more

Jump to
- Introductions & How to Use the Forum
- ↳ Welcome!
- ↳ Member Introductions
- ↳ How to Use the Forum
- ↳ Moderator Applications
- Welding Discussion
- ↳ Metal Cutting
- ↳ Tig Welding - Tig Welding Aluminum - Tig Welding Techniques - Aluminum Tig Welding
- ↳ Mig and Flux Core - gas metal arc welding & flux cored arc welding
- ↳ Stick Welding/Arc Welding - Shielded Metal Arc Welding
- ↳ Welding Forum General Shop Talk
- ↳ Welding Certification - Stick/Arc Welding, Tig Welding, Mig Welding Certification tests - Welding Tests of all kinds
- ↳ Welding Projects - Welding project Ideas - Welding project plans
- ↳ Product Reviews
- ↳ Fuel Gas Heating
- Welding Tips & Tricks
- ↳ Video Discussion
- ↳ Wish List
- Announcements & Feedback
- ↳ Forum News
- ↳ Suggestions, Feedback and Support
- Welding Marketplace
- ↳ Welding Jobs - Industrial Welding Jobs - Pipe Welding Jobs - Tig Welding Jobs
- ↳ Classifieds - Buy, Sell, Trade Used Welding Equipment
- Welding Resources
- ↳ Tradeshows, Seminars and Events
- ↳ The Welding Library
- ↳ Education Opportunities