I recently got some 7018 and 6010 to try out. The 7018 runs like a dream. The 6010 however is not working with me. Right now, I'm trying to just run a bead on flat 1/4" plate with 3/32 rod. I've tried everything from 50 to 70 Amps, 30% to 60% dig. I've held the arc long and short. I've held and angle anywhere from 90 to 45. Hot start from 30 to 45%.
Half the time, it's porous and ugly. The other half, there's no slag covering the bead at all. It's just looks chrome. Best bead I produced was with a whip and pause but I can't duplicate. I've done weaves as well but no circles. I'm aware that running 6010 is harder and my machine does have a setting for cellulosic (sp?) rods. Is there something I'm missing? Any general tips for running these rods?
Stick Welding Tips, Certification tests, machines, projects
- weldin mike 27
-
Weldmonger
-
Posts:
-
Joined:Fri Apr 01, 2011 10:59 pm
-
Location:Australia; Victoria
Hey,
I was told by my trade school teacher that you just put the rod in and let the consuming of it move you along. Therefore no real arc gap. I dont know if this is a real good way of doing it but its a start. I presume the "whip and pause" would be this motion with a slight move forward . Remembering to tho close that arc gap right up on the pause. I know when i tried to use 6011s with the same technique as a gp rod, i just got massive undercut with overroll. so there is a definite art to them.
Mick
I was told by my trade school teacher that you just put the rod in and let the consuming of it move you along. Therefore no real arc gap. I dont know if this is a real good way of doing it but its a start. I presume the "whip and pause" would be this motion with a slight move forward . Remembering to tho close that arc gap right up on the pause. I know when i tried to use 6011s with the same technique as a gp rod, i just got massive undercut with overroll. so there is a definite art to them.
Mick
I've tried keepin it tight. Got so tight I snuffed the arc and stuck the rod. I can see the puddle, the dig and the fill but it just doesn't seem to turn out right. Any idea what would cause no slag coverage?
Nick
I have heard that if you are using an inverter welder that that will sometimes cause issues with 6010s. Try picking up some 6011s. I have heard that they are slightly better with an inverter machine. You should be able to light up a 6010 3/32 at 40-70 amps no problem. One other thing you can try is dip the tip in water right before you light it up. I had an old pipeliner tell me that they used to take a handful of 6010s down to the creek when the inspector wasn't looking and give em a good soaking.
Be the monkey....
- weldin mike 27
-
Weldmonger
-
Posts:
-
Joined:Fri Apr 01, 2011 10:59 pm
-
Location:Australia; Victoria
Hey,
No, im sorry mate. I am merely repeating info i have in my head. Not much actual experience . Only thing maybe is to lay the rod over more than normal stick so that the weld naturally moves along as the rod burns. Keeping only enough pressure on it to keep the end of the rod in very close to the plate.????? maybe. sorry if i confuse you.
Ps I My Everlast power arc 200 has a separate port labled 6010. I think it has higher arc force built into that port.
Mick
No, im sorry mate. I am merely repeating info i have in my head. Not much actual experience . Only thing maybe is to lay the rod over more than normal stick so that the weld naturally moves along as the rod burns. Keeping only enough pressure on it to keep the end of the rod in very close to the plate.????? maybe. sorry if i confuse you.
Ps I My Everlast power arc 200 has a separate port labled 6010. I think it has higher arc force built into that port.
Mick
- weldin mike 27
-
Weldmonger
-
Posts:
-
Joined:Fri Apr 01, 2011 10:59 pm
-
Location:Australia; Victoria
Hey
I also have heard wetting them helps. Because they need a certain amount of moisture in the caoting to work. You didnt put them in the oven with your 7018s did you?
Mick
I also have heard wetting them helps. Because they need a certain amount of moisture in the caoting to work. You didnt put them in the oven with your 7018s did you?
Mick
Turns out my machine doesn't like alot of arc force with 6010. Here you can see some of the failures before I turned down the dig. The better beads were done with dig completely off.
Let me know what ya'll think
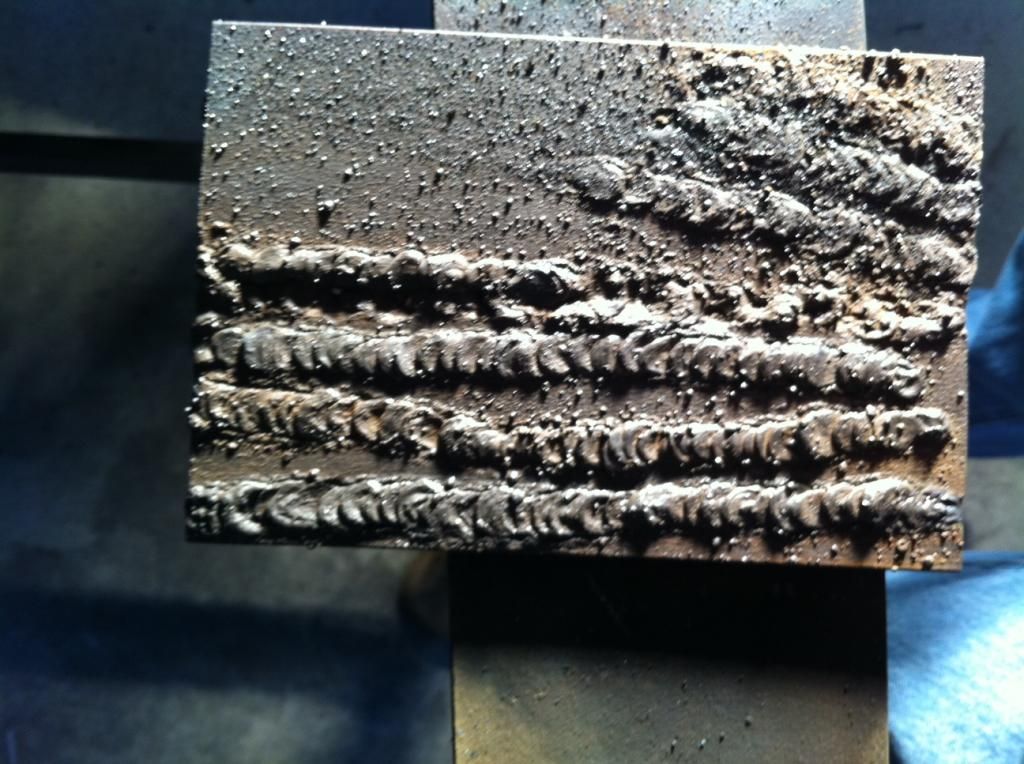
Let me know what ya'll think
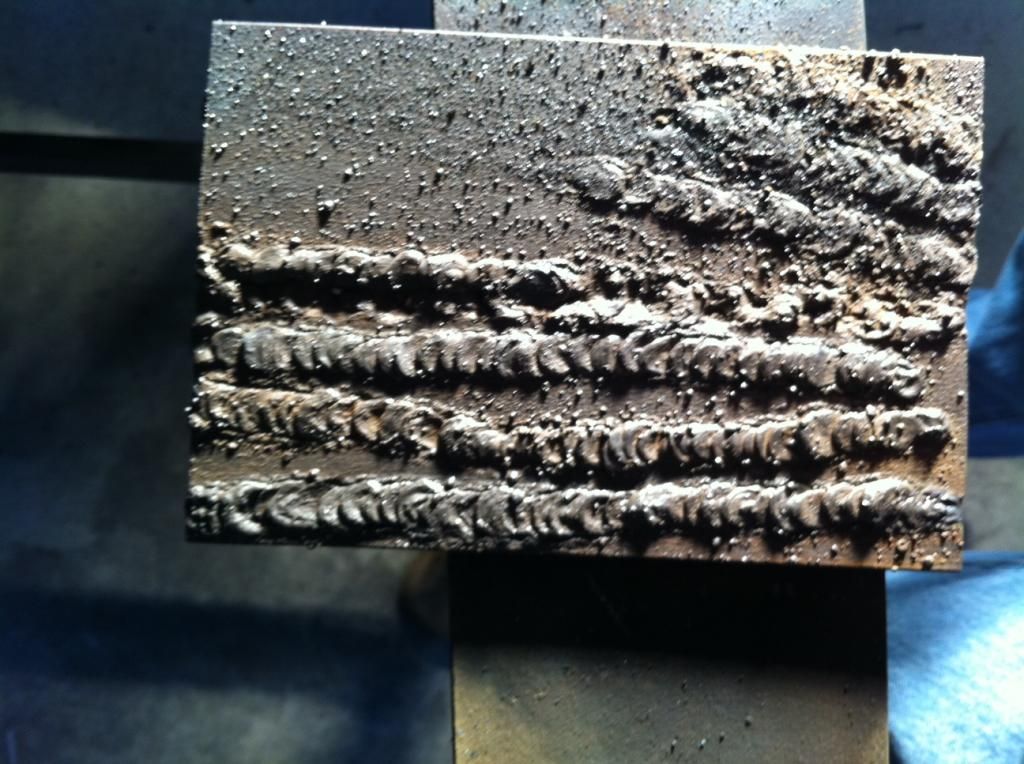
Nick
It was flat. Haven't attempted just running a stringer. The spatter was kinda built up from running several beads side by side. I believe it's normal for 6010 but if it is excessive what could be done to minimize it. I was holding the arc pretty tight already.Mrkil wrote:Are those done flat?
Tht seems like a lot of spatter. What does it look lile with a straight stringer bead? Not trying to be a smart a$$, i just mean a stright drag with no whip
Nick
- Otto Nobedder
-
Weldmonger
-
Posts:
-
Joined:Thu Jan 06, 2011 11:40 pm
-
Location:Near New Orleans
Try this, just for the hell of it. Turn it up to 85-90, strike up, draw a long-arc, and close in slowly, to give the rod a second or two to get hot near the end, then hold the rod at 15* (75* to the metal) slight drag while pushing straight down. Gently at first. The goal is to have the rod burn slightly behind the melting of the leading edge of the flux, so you are tight but not sticking. When this is working right, you'll find you can push down (not "in") fairly hard without sticking.
Arc force at 30% should be fine.
Since you're welding on flat plate, what you're doing is far closer to a cap than a root, so a whip/pause would be more appropriate, but at this point getting a consistent burn and a "feel" for the rod is more important. In a vee-groove root, you'd want the rod at 90*, as the vee itself is what the flux is landing on, but those details can be discussed once you can burn a rod consistantly.
Lord, this is hard to put in words!
Steve S
Arc force at 30% should be fine.
Since you're welding on flat plate, what you're doing is far closer to a cap than a root, so a whip/pause would be more appropriate, but at this point getting a consistent burn and a "feel" for the rod is more important. In a vee-groove root, you'd want the rod at 90*, as the vee itself is what the flux is landing on, but those details can be discussed once you can burn a rod consistantly.
Lord, this is hard to put in words!
Steve S
I'll give it a whirl but 85-90 seems pretty high for a 3/32 rod. I though I was starting to get a consistent burn. Are you only looking at the bottom 3 beads? Would this keep the spatter down?Otto Nobedder wrote:Try this, just for the hell of it. Turn it up to 85-90, strike up, draw a long-arc, and close in slowly, to give the rod a second or two to get hot near the end, then hold the rod at 15* (75* to the metal) slight drag while pushing straight down. Gently at first. The goal is to have the rod burn slightly behind the melting of the leading edge of the flux, so you are tight but not sticking. When this is working right, you'll find you can push down (not "in") fairly hard without sticking.
Arc force at 30% should be fine.
Since you're welding on flat plate, what you're doing is far closer to a cap than a root, so a whip/pause would be more appropriate, but at this point getting a consistent burn and a "feel" for the rod is more important. In a vee-groove root, you'd want the rod at 90*, as the vee itself is what the flux is landing on, but those details can be discussed once you can burn a rod consistantly.
Lord, this is hard to put in words!
Steve S
Just tryin to get a better idea of what I'm looking for
Nick
Yeah it is. Steve might have missed that you said 3/32. I run 3/32 anywhere from 30 to 75 amps but they run best around 60ish. Try wetting the tip like I suggested and make sure your polarity is right. I know that sounds dumb but it looks lime you are trying to run a 6010 on AC which doesn't work. How heavy is the base metal? I know that it would need to be a little extreme but it could be acting as a bit of a heat sink too.
Be the monkey....
Those last 3 beads were run at 50 amps. The base metal is 1/4" plate. The plate under it is also 1/4". I kinda keep that hanging off the side as I only have a wooden bench at the moment. Polarity DCEP.
I failed to mention that alot of that garbage on the top half of the plate was dust from slag and brushing. I didn't do anything to clean that side off.
I failed to mention that alot of that garbage on the top half of the plate was dust from slag and brushing. I didn't do anything to clean that side off.
Nick
Afsatcom.
Judging from the photo, those passes are pretty normal for someone just learning to weld cellulose rod. The pronounced ripples will be present with this type of puddle that solidifies quickly. The photo does confirm that you are exiting the puddle at times. Whipping is not necessary when welding a continuous pass in the flat position. Stay with a constant molten puddle (without skipping ahead) and you should do okay.
Alexa
Judging from the photo, those passes are pretty normal for someone just learning to weld cellulose rod. The pronounced ripples will be present with this type of puddle that solidifies quickly. The photo does confirm that you are exiting the puddle at times. Whipping is not necessary when welding a continuous pass in the flat position. Stay with a constant molten puddle (without skipping ahead) and you should do okay.
Alexa
I gave a couple goes at dragging but it didn't work out all that well. The flux would bind up on the plate and flop around a bit. I also made an attempt at keeping a tight steady arc but found it more difficult than whip and pause. The following was done with 65 amps and 30% arc force. I'll run a few rods under the faucet real quick and see how that turns out. I also gave the plate a quick wire wheeling so it's easier to look at.
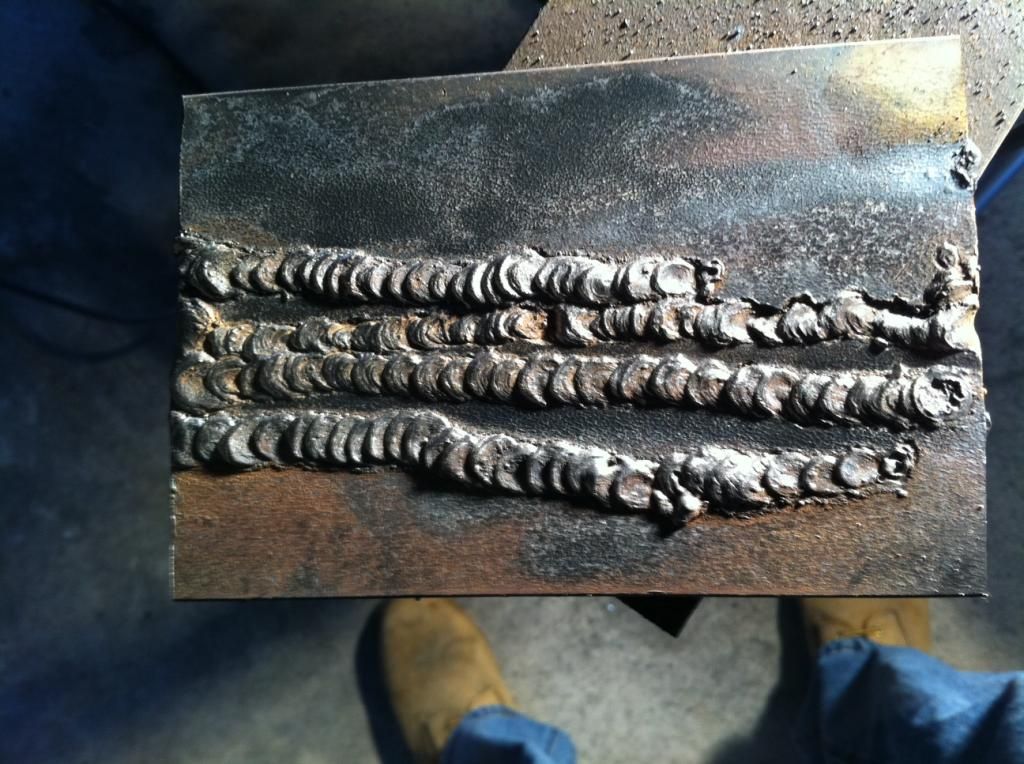
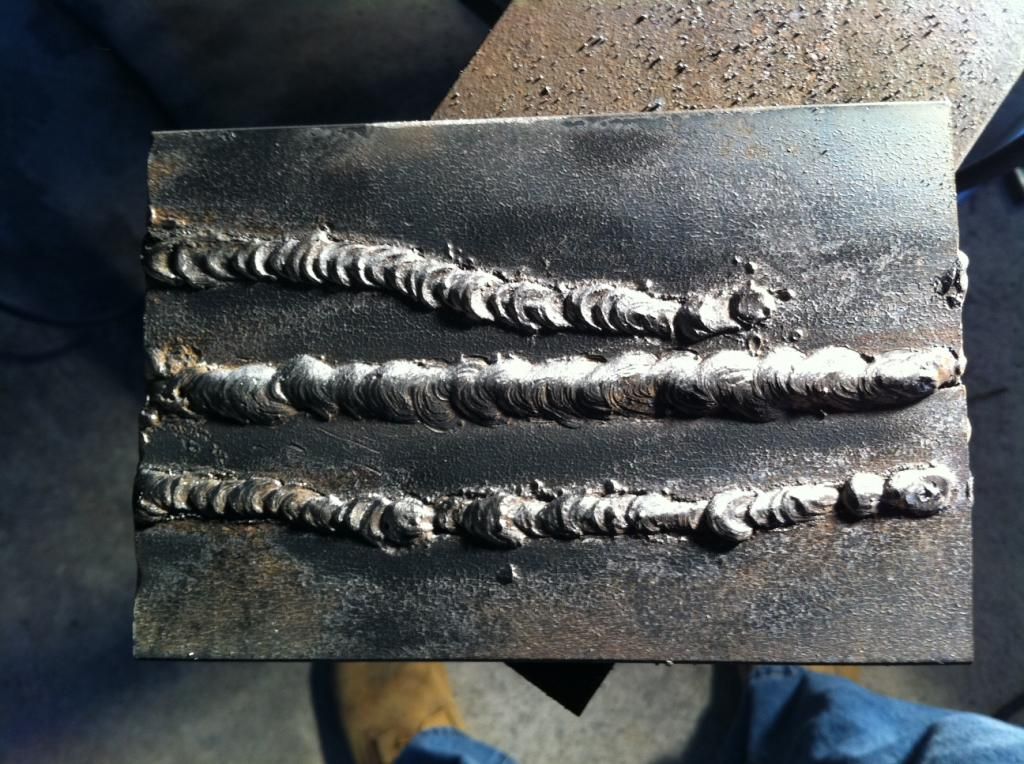
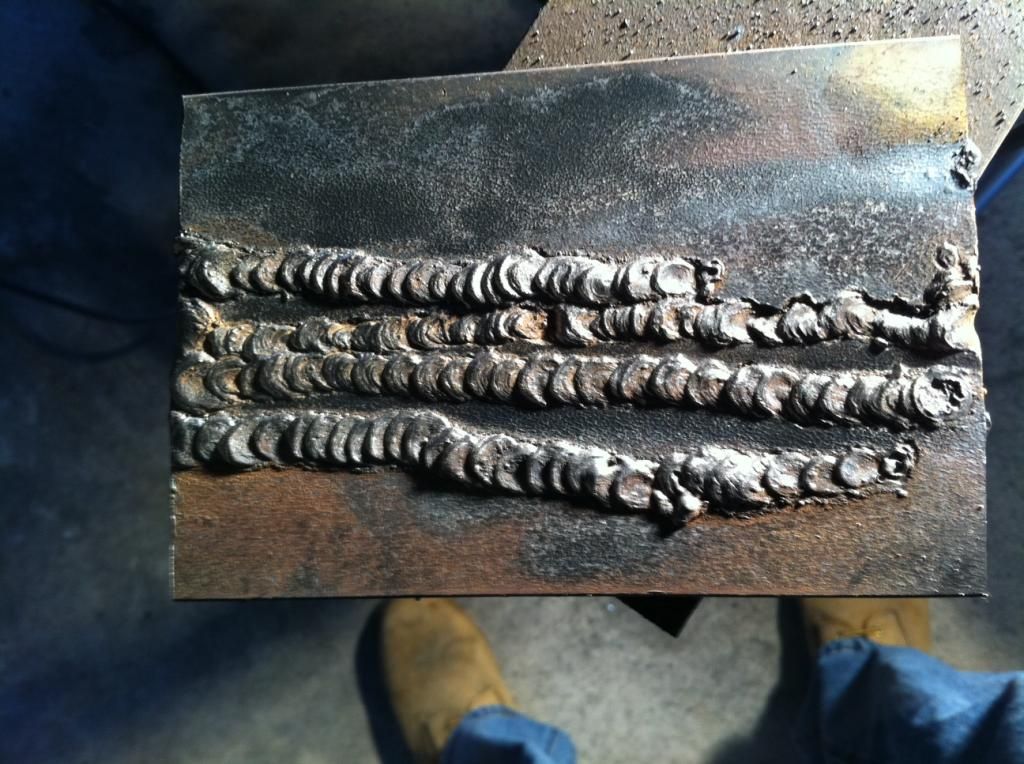
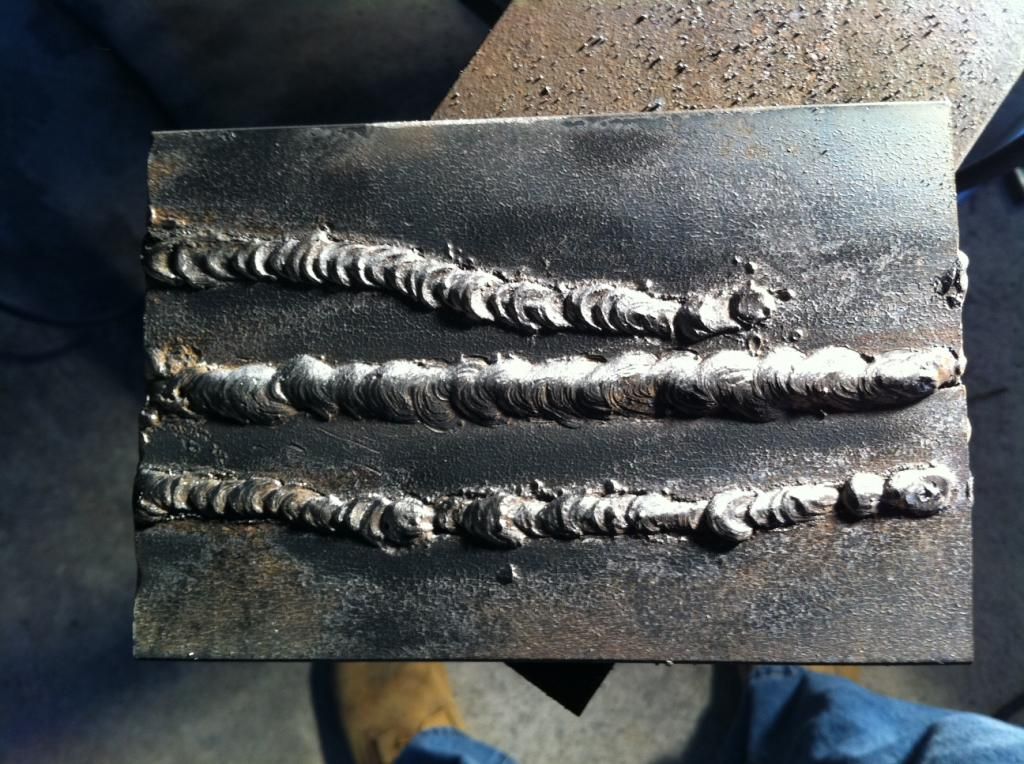
Nick
Here's a couple with the wet rods. They didn't really run much smoother but they did seem to burn a bit faster. No changes were made to the settings. I soaked em in the faucet then gave em about 10-15 mins to dry.
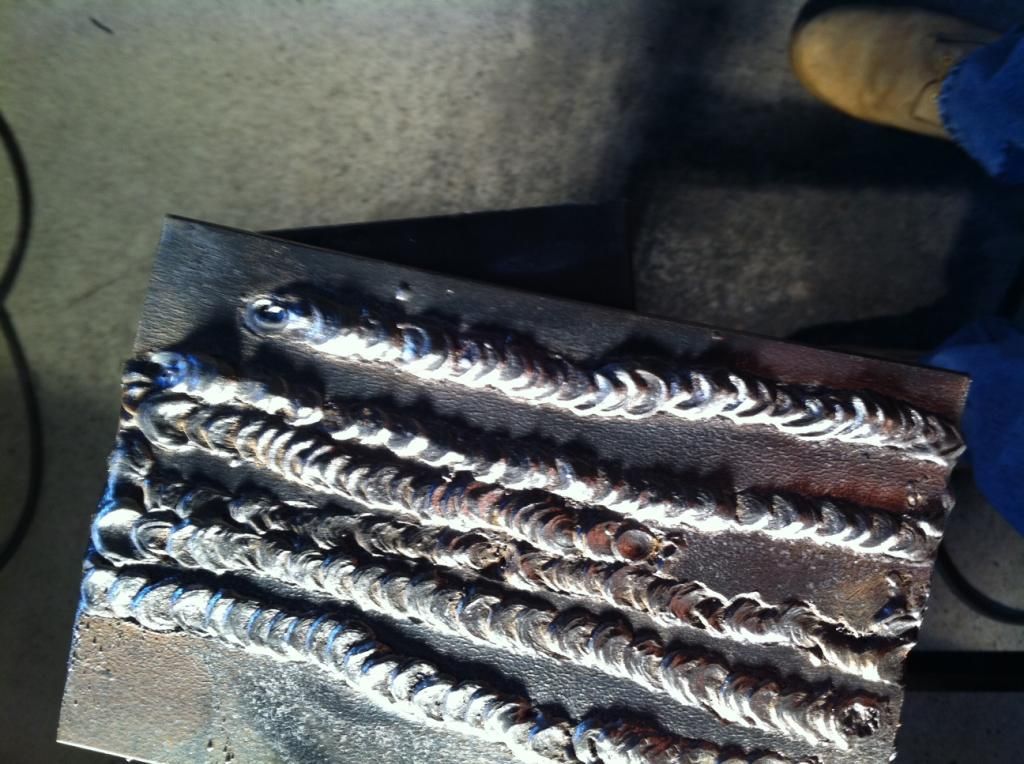
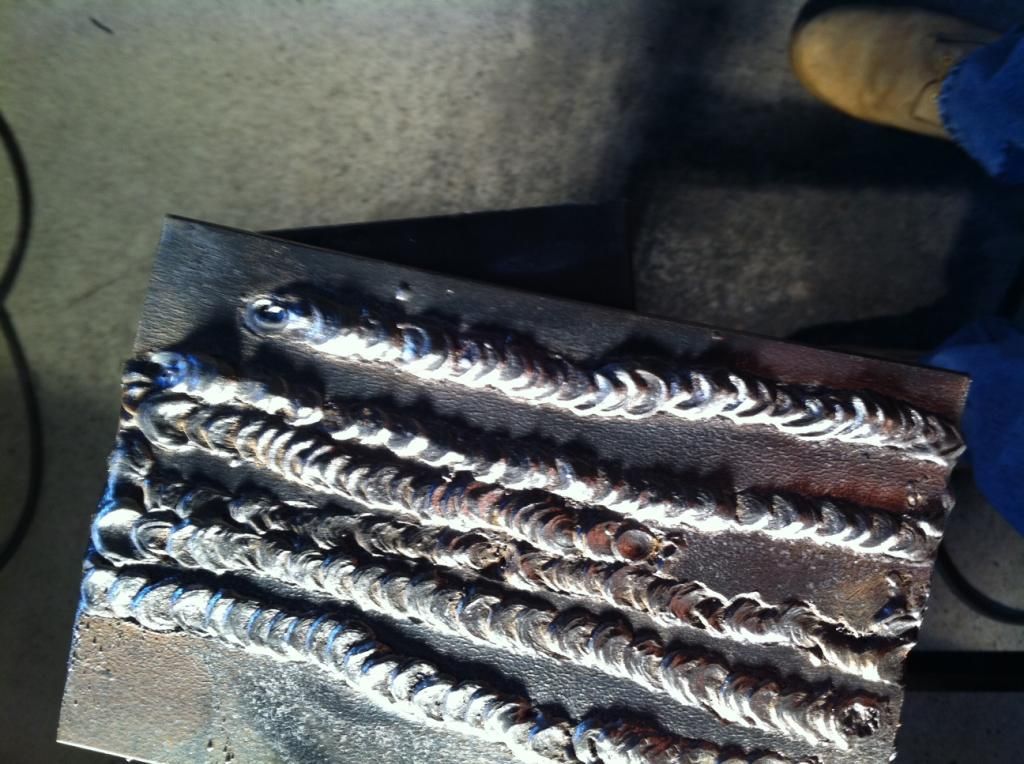
Nick
- Otto Nobedder
-
Weldmonger
-
Posts:
-
Joined:Thu Jan 06, 2011 11:40 pm
-
Location:Near New Orleans
I burn 1/8" 6010 at 105A. This way I can follow with 1/8" 7018 without changing settings. It works well for me, but might not be for everyone, which is why I said, "Just for the hell of it, try...", and I have never done 6010 "all the way", so my suggestion might not apply to beads on plate at all.nickn372 wrote:Yeah it is. Steve might have missed that you said 3/32. I run 3/32 anywhere from 30 to 75 amps but they run best around 60ish. Try wetting the tip like I suggested and make sure your polarity is right. I know that sounds dumb but it looks lime you are trying to run a 6010 on AC which doesn't work. How heavy is the base metal? I know that it would need to be a little extreme but it could be acting as a bit of a heat sink too.
I saw a few more consistent beads in the most recent photos, so something is beginning to click for the OP.
Time and practice...
Steve S
Yeah its starting to look better. Just try to maintain a consistent speed and dont whip and pause at all. If you do any motion on anything other than open root it should be a slight side to side or zig zag; not a whip n pause. Keep practicing try running about 60 amps with 1/4". Maybe try some lap joints if you have the spare steel, that sometimes helps. I just got done running 10 pounds of 6010 1/8 doing a repair job.
Be the monkey....
Well I tried running some joints today and found out first hand what fingernailing is. It would start out fine then about half way through the arc would wander to one plate or the other. Nothing I could do would get the bead back on track. I also noticed that the flux wasn't burning even and the arc seemed to be coming out of the side of the rod. It's a bit irritating when trying to learn with an already difficult rod. I guess I'll be soaking the rest of the box to try and salvage em.
Nick
Another thing I have learned is to not sacrifice for price. Buying cheap rods usually gives you what you paid for. I always buy lincoln electrodes. Bare wire and cut lengths is one thing but when you are buying rods or fluxcored wire you cant sacrifice quality for price or you end up with crap for welds. Keep tryin dude and keep us up to date!
Be the monkey....
Usually 6010's will perform just fine with moisture that is present in the air (in NC anyway). To help your learning curve, keep arc force at 30% and try a crescent motion )))))))))))))))))) or a D motion DDDDDDDDDDDD (overlapping of course) or a circular motion and work on keeping your beads straight. Once you are consistent with your beads then start with the whip and pause. When you step out on your whip look for the puddle to solidify before moving back for your pause. Usually about 75% of my students have to run a few beads with a regular motion before starting to whip. This will also help you tweak your amp selection instead of being all over the map.
Kevin
Kevin
Not to sound smug but are you using DC + ?AFSATCOM wrote:Turns out my machine doesn't like alot of arc force with 6010. Here you can see some of the failures before I turned down the dig. The better beads were done with dig completely off.
Let me know what ya'll think
It's been awhile so I can't say for certain that I didn't forget to switch the leads around after working with tig again. I am quite certain though that at least some of the attempts were done at the correct polarity.
I've been out of it for a bit due to a deployment. While I was down range I had a few projects to do. I got ahold of a trailblazer 302d and some lincoln 6010s. I gotta say that I am thouroughly convinced that the rods I have are garbage. Half the time the flux wasn't wanting to burn off or fingernailing on me. I will get some more rods and have another go at it when I get setlled in back home again. I got a powermax 45 on the way as well.
I've been out of it for a bit due to a deployment. While I was down range I had a few projects to do. I got ahold of a trailblazer 302d and some lincoln 6010s. I gotta say that I am thouroughly convinced that the rods I have are garbage. Half the time the flux wasn't wanting to burn off or fingernailing on me. I will get some more rods and have another go at it when I get setlled in back home again. I got a powermax 45 on the way as well.
Nick
Ultralow787
- Ultralow787
-
Guide
-
Posts:
-
Joined:Fri Apr 29, 2011 11:30 pm
-
Location:Ontario, Canada
The beads don't look all that bad for 6010 to me...especially the later ones you posted.
One thing that surprised me was that a small Miller Maxstar 140 or 150 will not run 6010 electrodes at all. We could not even get the arc to light up. A friend told me his 150 would not run them and I couldn't believe it. We tried them on the 140 at school and no way. The same little inverter runs 7018 like nothing!
What kind of machine were you using originally. I know you mentioned the Trail blazer seemed to work well.
One thing that surprised me was that a small Miller Maxstar 140 or 150 will not run 6010 electrodes at all. We could not even get the arc to light up. A friend told me his 150 would not run them and I couldn't believe it. We tried them on the 140 at school and no way. The same little inverter runs 7018 like nothing!
What kind of machine were you using originally. I know you mentioned the Trail blazer seemed to work well.
Perfection is impossible, but if you strive for perfection, excellence is obtainable!
1983 Canox "Sparkler" 225 AC Stick Welder
Hobart 210 MVP MIG Welder
Harris "Spitfire" Oxy-Acetylene Set
1983 Canox "Sparkler" 225 AC Stick Welder
Hobart 210 MVP MIG Welder
Harris "Spitfire" Oxy-Acetylene Set
Return to “Stick Welding/Arc Welding - Shielded Metal Arc Welding”
Jump to
- Introductions & How to Use the Forum
- ↳ Welcome!
- ↳ Member Introductions
- ↳ How to Use the Forum
- ↳ Moderator Applications
- Welding Discussion
- ↳ Metal Cutting
- ↳ Tig Welding - Tig Welding Aluminum - Tig Welding Techniques - Aluminum Tig Welding
- ↳ Mig and Flux Core - gas metal arc welding & flux cored arc welding
- ↳ Stick Welding/Arc Welding - Shielded Metal Arc Welding
- ↳ Welding Forum General Shop Talk
- ↳ Welding Certification - Stick/Arc Welding, Tig Welding, Mig Welding Certification tests - Welding Tests of all kinds
- ↳ Welding Projects - Welding project Ideas - Welding project plans
- ↳ Product Reviews
- ↳ Fuel Gas Heating
- Welding Tips & Tricks
- ↳ Video Discussion
- ↳ Wish List
- Announcements & Feedback
- ↳ Forum News
- ↳ Suggestions, Feedback and Support
- Welding Marketplace
- ↳ Welding Jobs - Industrial Welding Jobs - Pipe Welding Jobs - Tig Welding Jobs
- ↳ Classifieds - Buy, Sell, Trade Used Welding Equipment
- Welding Resources
- ↳ Tradeshows, Seminars and Events
- ↳ The Welding Library
- ↳ Education Opportunities