Tig welding tips, questions, equipment, applications, instructions, techniques, tig welding machines, troubleshooting tig welding process
- jumpinjackflash
-
Guide
-
Posts:
-
Joined:Sun Feb 02, 2014 6:14 pm
-
Location:Near Mt Airy
I am still having trouble getting the weld that looks right. I was just wanting to see if anyone has a welded piece or a scrap tube they could show me what a decent weld on this small stuff should look like. I have been using 1/16" Ceriated tungsten, gas lens and .035" ER70-s2 with always a 3/16" or wider weld pool. Or at least I can see that the filler has wet out that far. When I try and get the weld area tighter.. with the least amount amperage to make a puddle..it just doesn't look like a sound weld. Back to the shop to burn some more filler....and practice. I will experiment with a .040" tungsten and see where that leads. I always want to do the easy stuff...I like the punishment. Any advice or pointers VERY welcome.
Building an airplane is at times somewhat like a divorce.....with the exception that she doesn't leave
J.J. Flash
J.J. Flash
- Superiorwelding
-
Weldmonger
-
Posts:
-
Joined:Thu Jan 24, 2013 10:13 pm
-
Location:Eddy, TX
jumpinjackflash,
Can you get a picture up? I will give it a whirl if I know exactly what it is.
Can you get a picture up? I will give it a whirl if I know exactly what it is.
Instagram- @superiorwelding/@learntotig
Twitter- @_JonathanLewis
https://www.learntotig.com
https://www.superiorweldandfab.com
https://www.youtube.com/+SuperiorWeldin ... ATHANLEWIS
Twitter- @_JonathanLewis
https://www.learntotig.com
https://www.superiorweldandfab.com
https://www.youtube.com/+SuperiorWeldin ... ATHANLEWIS
I have some 1/4" 0.035 304 coming on Tuesday and I'll give it a whirl. I don't have any 4130 that small, but I have some 1/2" 0.024 that I can weld up.
One tip is the make a purge dam out of aluminum foil and put it behind where you are welding. That will trap some argon and keep the area clean.
One tip is the make a purge dam out of aluminum foil and put it behind where you are welding. That will trap some argon and keep the area clean.
- jumpinjackflash
-
Guide
-
Posts:
-
Joined:Sun Feb 02, 2014 6:14 pm
-
Location:Near Mt Airy
OK I went out into the shop today and ran beads on a piece of .065" tube to gain a bit of confidence. Then went for some scrap tubing in 1/4" molly and some 050" molly plate. The best welds I could get were with 60 PPS. Had some good beads with no pulse and cooled between passes. Tried to keep the weld bead small as possible and tight arc. Welding with gas lens... .060" ceriated...pure argon @ 15 CFH ER70-s2 .035" . It always comes down to if I get the puddle looking good and getting it to take filler it seems it is too hot of a weld. Grey with no color. When it did weld good....I was either at the end of a weld or just some random luck. Still looking at a steep learning curve I guess. Wish I was near someone capable that would accept a donation for some help....I hate to admit but I am lost in the forest. Gotta be something stupid simple to fix me. Seems I get close with this and then something just goes away. Thoroughly confused. I did try upsizing to a #8 cup and that helped a bit. Not even going to show the tube junction I tried to weld....very wide 3/16"weld...but had color and didn't look burnt.
- Attachments
-
- best I could get on 035" tube
- PANA0036.JPG (83.63 KiB) Viewed 1154 times
-
- too hot
- PANA0035.JPG (81.68 KiB) Viewed 1154 times
-
- decent bead but getting hot near the end
- PANA0034.JPG (72.75 KiB) Viewed 1154 times
Building an airplane is at times somewhat like a divorce.....with the exception that she doesn't leave
J.J. Flash
J.J. Flash
- Superiorwelding
-
Weldmonger
-
Posts:
-
Joined:Thu Jan 24, 2013 10:13 pm
-
Location:Eddy, TX
jumpinjackflash,
I am not sure I understand exactly what we are after, but sometimes I have those moments. I went out and found some 5/8" O.D x like.020ish wall pipe and quickly played around. My settings; 20 amps (used 11 average) 3/32" 1.5%Lanthanated, stubby CK gas lens, #7 cup and 15 CFH, using .035 ER70S-6. The bottom weld is how I would normally weld with me backing off amps in the middle. I am assuming you are wanting a smaller weld so I was trying different techniques on the others. Critique mine all you want I only spent a few minutes on it and got to thinking what exactly are you after? Do you want a smaller bead because you think it is to much weld or are you getting it to "hot" and burning through the tube?
I am not sure I understand exactly what we are after, but sometimes I have those moments. I went out and found some 5/8" O.D x like.020ish wall pipe and quickly played around. My settings; 20 amps (used 11 average) 3/32" 1.5%Lanthanated, stubby CK gas lens, #7 cup and 15 CFH, using .035 ER70S-6. The bottom weld is how I would normally weld with me backing off amps in the middle. I am assuming you are wanting a smaller weld so I was trying different techniques on the others. Critique mine all you want I only spent a few minutes on it and got to thinking what exactly are you after? Do you want a smaller bead because you think it is to much weld or are you getting it to "hot" and burning through the tube?
- Attachments
-
- small welds.JPG (119.65 KiB) Viewed 1145 times
Instagram- @superiorwelding/@learntotig
Twitter- @_JonathanLewis
https://www.learntotig.com
https://www.superiorweldandfab.com
https://www.youtube.com/+SuperiorWeldin ... ATHANLEWIS
Twitter- @_JonathanLewis
https://www.learntotig.com
https://www.superiorweldandfab.com
https://www.youtube.com/+SuperiorWeldin ... ATHANLEWIS
- jumpinjackflash
-
Guide
-
Posts:
-
Joined:Sun Feb 02, 2014 6:14 pm
-
Location:Near Mt Airy
I am trying to get some progress towards welding tube junctions together without a giant weld area. I was told that a weld that was much larger than the thickness of the material being joined was too much heat involved. So I am trying to get my welds down and small. Then I will try some "T" joints again. I have not tried to purge the inside...just out on the table with all this. Thanks for welding some really thin tube...looks great. So if having a weld that is 1/8 to 3/16 wide on this stuff will I be OK to get some straw color and the bead is flat or raised up a little? Just can't get stacking going on with this small tube. Or do I need to even worry with that? Just get it welded together without burning it up and call it good?
Thanks again for helping me....
Thanks again for helping me....
Building an airplane is at times somewhat like a divorce.....with the exception that she doesn't leave
J.J. Flash
J.J. Flash
I don't see anything wrong with what Superior posted above but if you want to narrow your bead up and make the HAZ smaller you could pulse the weld.... I am using the pulse feature more on thin stainless all the time, great penetration and arc control. You could also try some .040" Tungsten, I also prefer the Gas Lens setup.
I weld stainless, stainless and more stainless...Food Industry, sanitary process piping, vessels, whatever is needed, I like to make stuff.
ASME IX, AWS 17.1, D1.1
Instagram #RNHFAB
ASME IX, AWS 17.1, D1.1
Instagram #RNHFAB
Here's some 1/4" OD x 0.035" wall 304 SS. I didn't have any 4130 in that size. Here are a few tips after doing this exercise.
A cheater is critical for me when welding stuff this small. I'm using a +2.00 in my hood.
I used 0.035" 308L rod. ER70S-2 won't flow as nicely, but 0.035" is a good size.
I set the machine at 45 amps and used the pedal. My machine does not have pulse. I do not pulse with my foot. Nice steady current and backing off as the piece gets hotter to keep the puddle a consistent width.
Below is a picture of my torch setup. 9-series flex loc with a gas lens, #7 cup, 1/16" 2% Lanthanated tungsten, 15 CFH, pure argon. I probably could have put a longer taper on the electrode, but the arc was stable with the electrode as-is. A 0.040" electrode probably would have lit up a little easier, but again, I didn't have any trouble establishing an arc.
The challenge here isn't so much the wall thickness, it's the diameter and how quickly the torch angle needs to change to keep everything shielded and keep the bead looking consistent. That's just practice. Keep running beads and work on consistent bead width, dip spacing, dip amount, and travel speed.
Hope this helps!
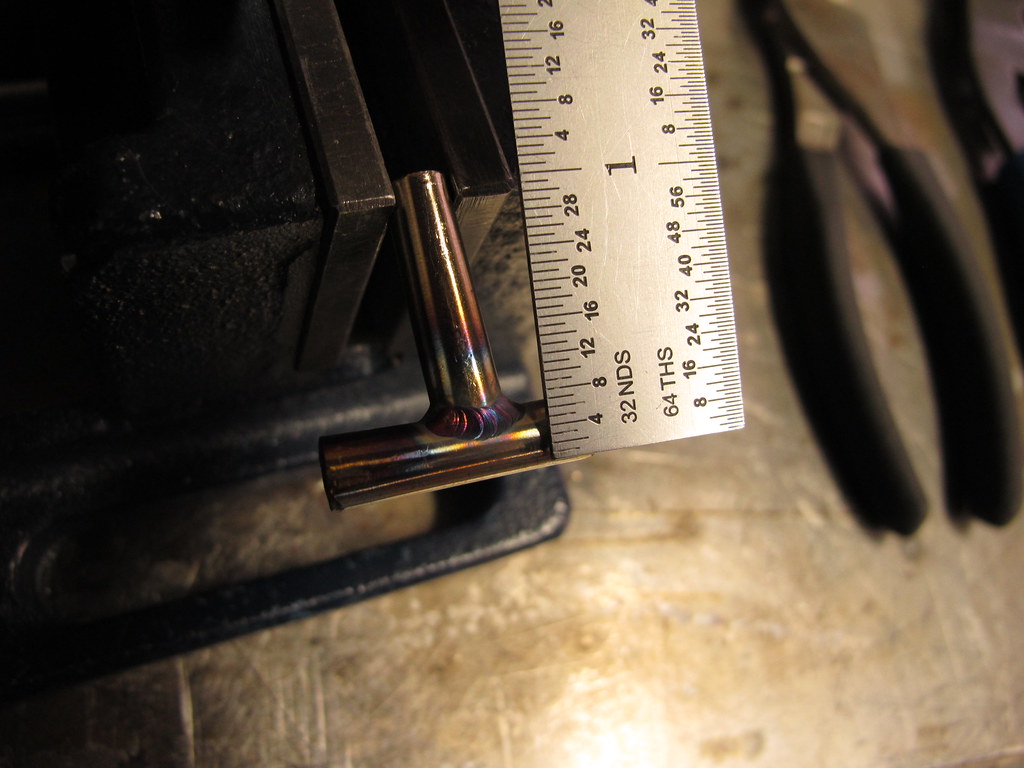
1/4" OD 304 SS by Zanconato Custom Cycles, on Flickr

Rep yer torch by Zanconato Custom Cycles, on Flickr
A cheater is critical for me when welding stuff this small. I'm using a +2.00 in my hood.
I used 0.035" 308L rod. ER70S-2 won't flow as nicely, but 0.035" is a good size.
I set the machine at 45 amps and used the pedal. My machine does not have pulse. I do not pulse with my foot. Nice steady current and backing off as the piece gets hotter to keep the puddle a consistent width.
Below is a picture of my torch setup. 9-series flex loc with a gas lens, #7 cup, 1/16" 2% Lanthanated tungsten, 15 CFH, pure argon. I probably could have put a longer taper on the electrode, but the arc was stable with the electrode as-is. A 0.040" electrode probably would have lit up a little easier, but again, I didn't have any trouble establishing an arc.
The challenge here isn't so much the wall thickness, it's the diameter and how quickly the torch angle needs to change to keep everything shielded and keep the bead looking consistent. That's just practice. Keep running beads and work on consistent bead width, dip spacing, dip amount, and travel speed.
Hope this helps!
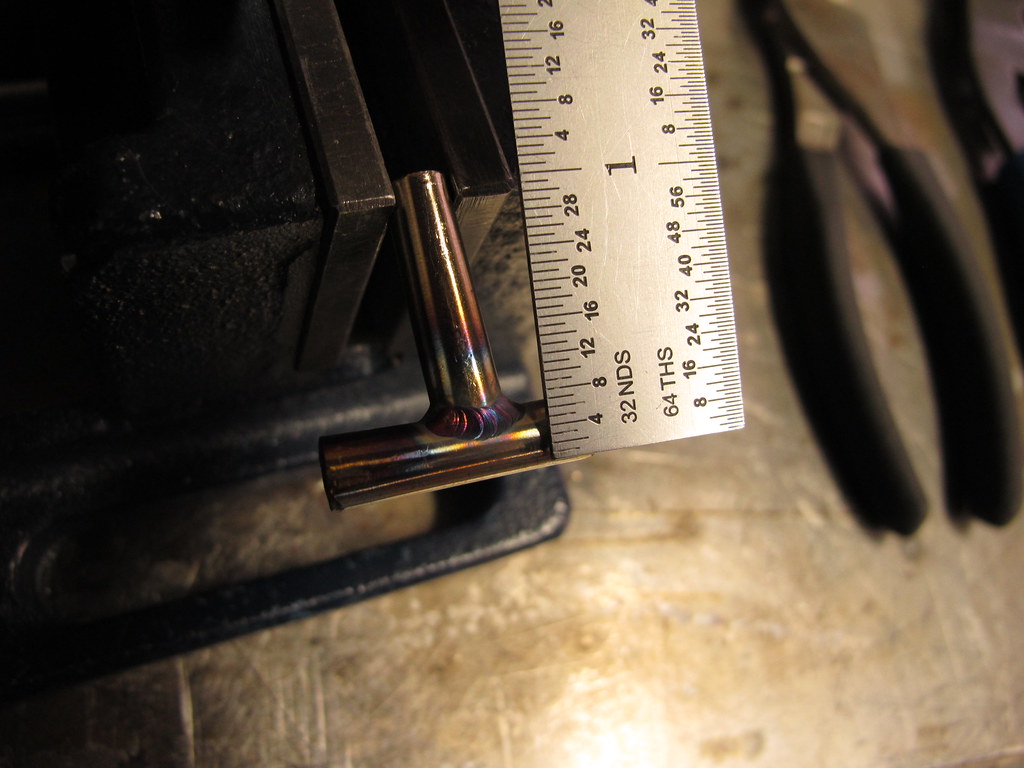
1/4" OD 304 SS by Zanconato Custom Cycles, on Flickr

Rep yer torch by Zanconato Custom Cycles, on Flickr
- jumpinjackflash
-
Guide
-
Posts:
-
Joined:Sun Feb 02, 2014 6:14 pm
-
Location:Near Mt Airy
If I made a weld like that .... I would probably crap my pants ! That is simply beautiful and exactly what I am trying to get myself to be able to do in the future. So a 3/32" to 1/8" wide weld bead is OK on this thin , small stuff? Now I think I may be able to try and make some good practice. I was trying to get a bead down to no wider than 3/32"- shooting for a nice 1/16" bead. That is crazy for me to try and do that. I did make a bunch of tubes notched on the mill for practice....want to run some beads first...Jody's steel drill for me. My welds need to be sound and strong and I am still concerned about the color of some of them...some grey and chalky looking. Most all the welds I see on the web are nice shiny puddles and some with colors and metal not blued out far from the weld area. Like Jody said...tight arc length, filler hot end inside gas shield, and good torch angle. Let me know on the color of the weld puddle with molly.....still see some that are silver looking...but they are shiny then some with a rainbow color and a nice puddle. Just trying to learn from the pro's who know how. Thank you to all that have took time for me...it has helped me a ton!
On a side note...could my weld craft w-17 torch that came with the machine be a bad influence on me try to weld what I want?
On a side note...could my weld craft w-17 torch that came with the machine be a bad influence on me try to weld what I want?
Building an airplane is at times somewhat like a divorce.....with the exception that she doesn't leave
J.J. Flash
J.J. Flash
Happy to help! Yeah, I would say if you can keep the bead width closer to 1/16", that would be ideal. Mine might have been a little wide.
With 4130 and ER70S-2, you can still get nice shiny welds with good gas coverage. You are keeping the torch over weld during the post flow, right?
The 17 torch is totally fine. The smaller torch is nice, but not necessary.
With 4130 and ER70S-2, you can still get nice shiny welds with good gas coverage. You are keeping the torch over weld during the post flow, right?
The 17 torch is totally fine. The smaller torch is nice, but not necessary.
- jumpinjackflash
-
Guide
-
Posts:
-
Joined:Sun Feb 02, 2014 6:14 pm
-
Location:Near Mt Airy
Yes...post flow is a habit as well as tapering off slow...I try to weave the torch a small bit like in Jody's vids tapering off. I think I need to slow down and try to take some time when welding this...always afraid of getting the metal too hot or heated too long and ruining the project. If it winds up brittle and hardened...it's junk then. I just don't exactly know my limits with heat vs. time during a weld like this. I know it needs to be welded slower. Good to know on my torch. About welding gear spent out for right now...plus uncertainty of my job keeping funds tight. Thanks again and all pointers happily accepted. I was beginning to wonder if I would ever be able to get some decent weld action going on out of me.
Building an airplane is at times somewhat like a divorce.....with the exception that she doesn't leave
J.J. Flash
J.J. Flash
Return to “Tig Welding - Tig Welding Aluminum - Tig Welding Techniques - Aluminum Tig Welding”
Jump to
- Introductions & How to Use the Forum
- ↳ Welcome!
- ↳ Member Introductions
- ↳ How to Use the Forum
- ↳ Moderator Applications
- Welding Discussion
- ↳ Metal Cutting
- ↳ Tig Welding - Tig Welding Aluminum - Tig Welding Techniques - Aluminum Tig Welding
- ↳ Mig and Flux Core - gas metal arc welding & flux cored arc welding
- ↳ Stick Welding/Arc Welding - Shielded Metal Arc Welding
- ↳ Welding Forum General Shop Talk
- ↳ Welding Certification - Stick/Arc Welding, Tig Welding, Mig Welding Certification tests - Welding Tests of all kinds
- ↳ Welding Projects - Welding project Ideas - Welding project plans
- ↳ Product Reviews
- ↳ Fuel Gas Heating
- Welding Tips & Tricks
- ↳ Video Discussion
- ↳ Wish List
- Announcements & Feedback
- ↳ Forum News
- ↳ Suggestions, Feedback and Support
- Welding Marketplace
- ↳ Welding Jobs - Industrial Welding Jobs - Pipe Welding Jobs - Tig Welding Jobs
- ↳ Classifieds - Buy, Sell, Trade Used Welding Equipment
- Welding Resources
- ↳ Tradeshows, Seminars and Events
- ↳ The Welding Library
- ↳ Education Opportunities