Page 1 of 2
Re: Thin aluminum
Posted: Fri Sep 01, 2017 4:06 am
by AndersK
LtBadd wrote:
AndersK, you snapped it off before starting the weld!!

So you really think I can weld?
It actually needed 2 or three bends to snap off

Re: Thin aluminum
Posted: Sun Sep 17, 2017 6:17 pm
by Dalzani
Hello all again.
Trying some overlaps on thin aluminum 1.5mm. I don´t know why but seems to be much more difficult then a butt joint using the same thickness. Probably the weld is good but it is VERY ugly. What i´m doing wrong?
By the way... 60A for the bead.
Thanks all.
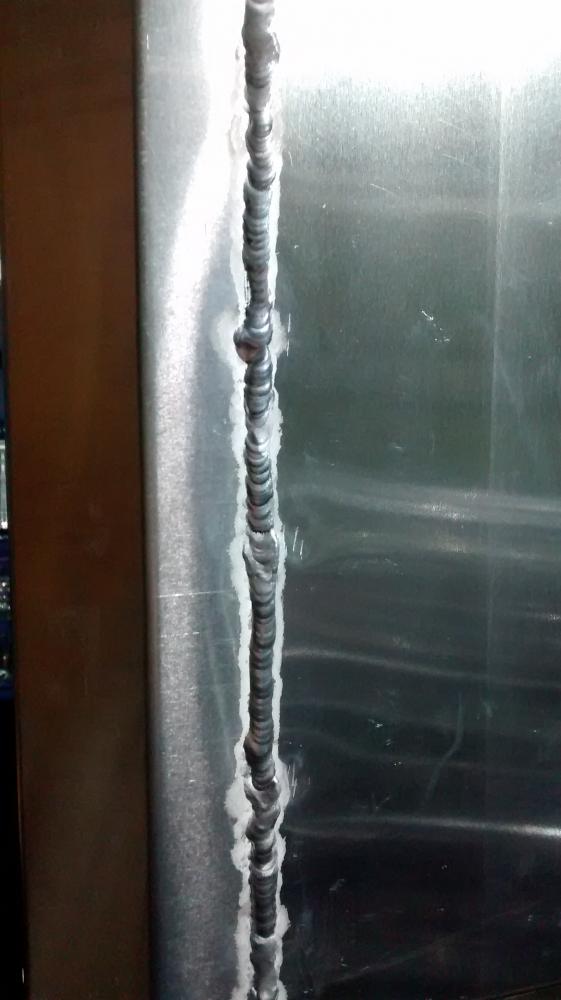
- Overlap bead
- overlap.jpg (48.83 KiB) Viewed 1767 times
Re: Thin aluminum
Posted: Sun Sep 17, 2017 6:50 pm
by motox
the sheets need to be clamped as so the edge does not lift or warp.
use a backer and tack often.
if the edge lifts heat gets under the edge and melts it away.
hope this help some
craig
Re: Thin aluminum
Posted: Sun Sep 17, 2017 7:00 pm
by Dalzani
No clamps was used. And just a few tacks 3 or 4 in a 35 cm extension. Next time I´ll double the tacks and buy some long clamps. You are sure a did a lot of deviations to refill the burned edges.
Thanks.
Re: Thin aluminum
Posted: Mon Sep 18, 2017 3:36 am
by AndersK
No too bad, just need more time to maintain consistent speed.
When welding long flat surfaces I use a small piece of fire blanket that I fold to about 4 layers. Rest your palm at it and you won't get burned and it helps you slide along easier.
Re: Thin aluminum
Posted: Mon Sep 18, 2017 6:01 pm
by Dalzani
AndersK, good ideia.
And what about "Tig Finger"? Anyone knows the material used?
Edited...
I did not see any penetration on the back side of aluminum. Using 60A and was already very difficult to avoid burning the edges.
Is this right?
Thanks.