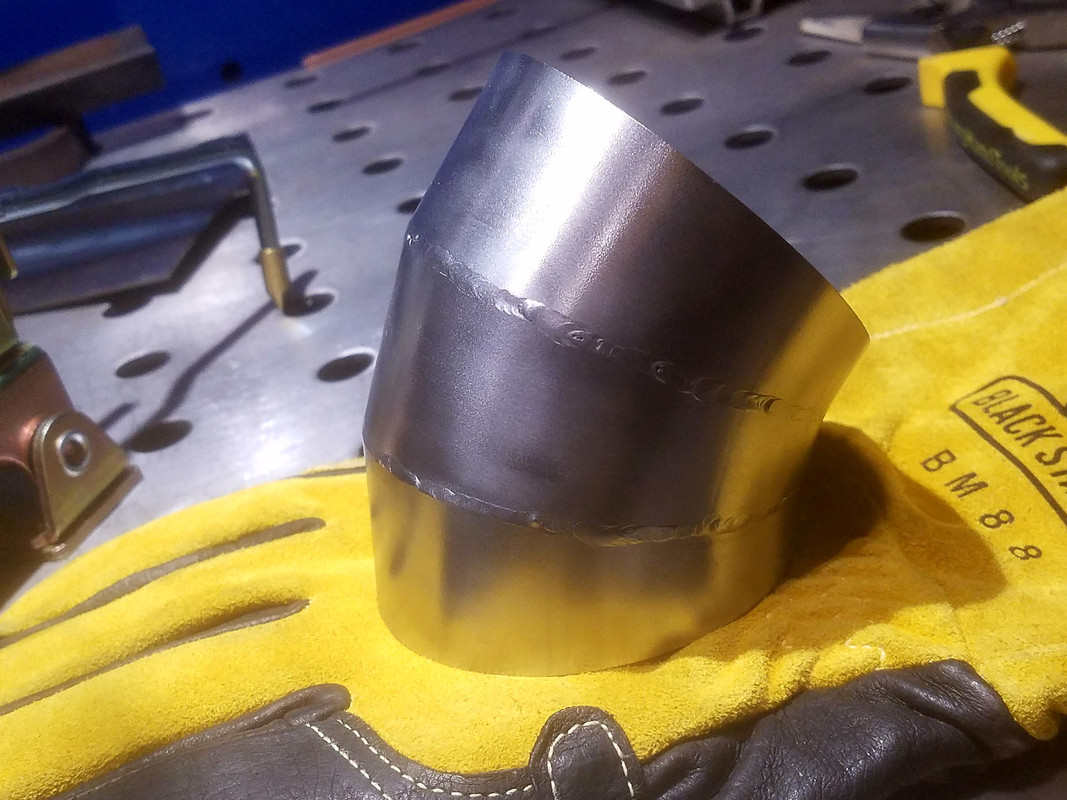
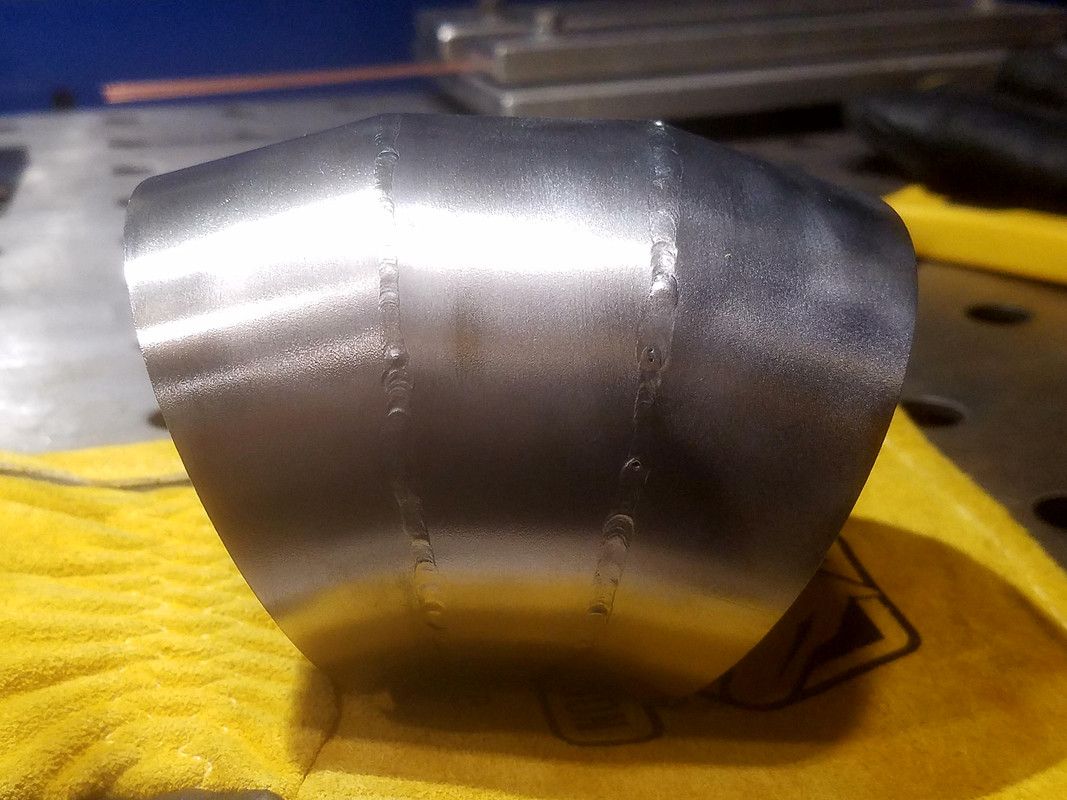
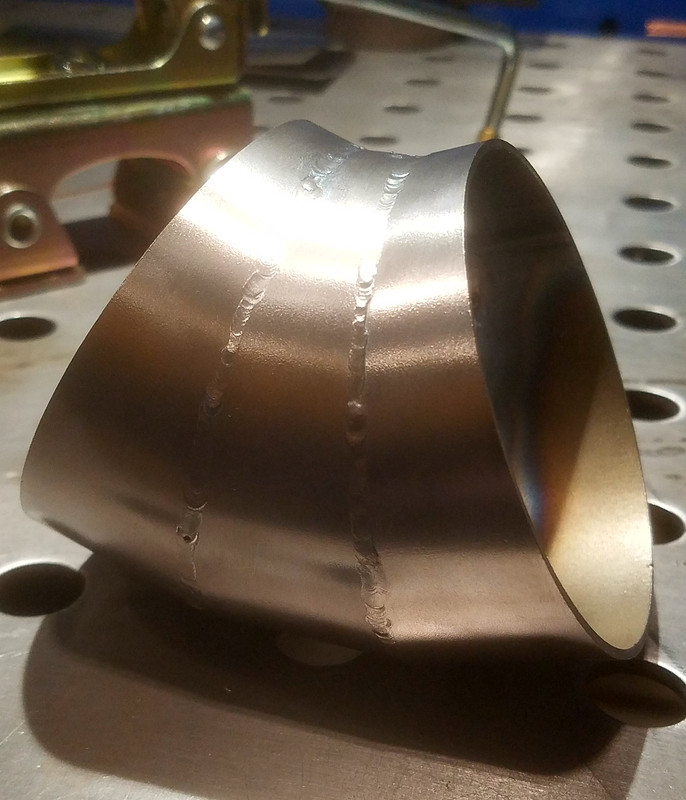
yeah its noticeable with the cold tack on tack.
I can weld up the drilled hole after it cools?cj737 wrote: ↑Sun Apr 10, 2022 6:36 pm Kokodan - when you weld up tubing at both ends, drill a small vent hole in the intersecting tube beneath the coping or along the length of the tube. The heat and gas from welding needs a place to vacate else you can find your closing bead blowing out from internal pressure.
Yep. And yup. Whichever you prefer.Kodokan wrote: ↑Mon Apr 11, 2022 4:30 pmI can weld up the drilled hole after it cools?cj737 wrote: ↑Sun Apr 10, 2022 6:36 pm Kokodan - when you weld up tubing at both ends, drill a small vent hole in the intersecting tube beneath the coping or along the length of the tube. The heat and gas from welding needs a place to vacate else you can find your closing bead blowing out from internal pressure.
Okay to leave the last bit of weld open until it cools, then go back and finish (instead of drilling a hole)?
Thanks! I don't need more injuries.
yes sort of. kinda depends on the situation. if the weld has a good fit up then the gap may be far to small to vent the air. plus as you weld along, the heat gets higher and the gap gets smaller, making the air speed go up so you can have quite a fast bit of air coming out right at your weld puddle.Kodokan wrote: ↑Mon Apr 11, 2022 4:30 pmI can weld up the drilled hole after it cools?cj737 wrote: ↑Sun Apr 10, 2022 6:36 pm Kokodan - when you weld up tubing at both ends, drill a small vent hole in the intersecting tube beneath the coping or along the length of the tube. The heat and gas from welding needs a place to vacate else you can find your closing bead blowing out from internal pressure.
Okay to leave the last bit of weld open until it cools, then go back and finish (instead of drilling a hole)?
Thanks! I don't need more injuries.
Return to “Tig Welding - Tig Welding Aluminum - Tig Welding Techniques - Aluminum Tig Welding”