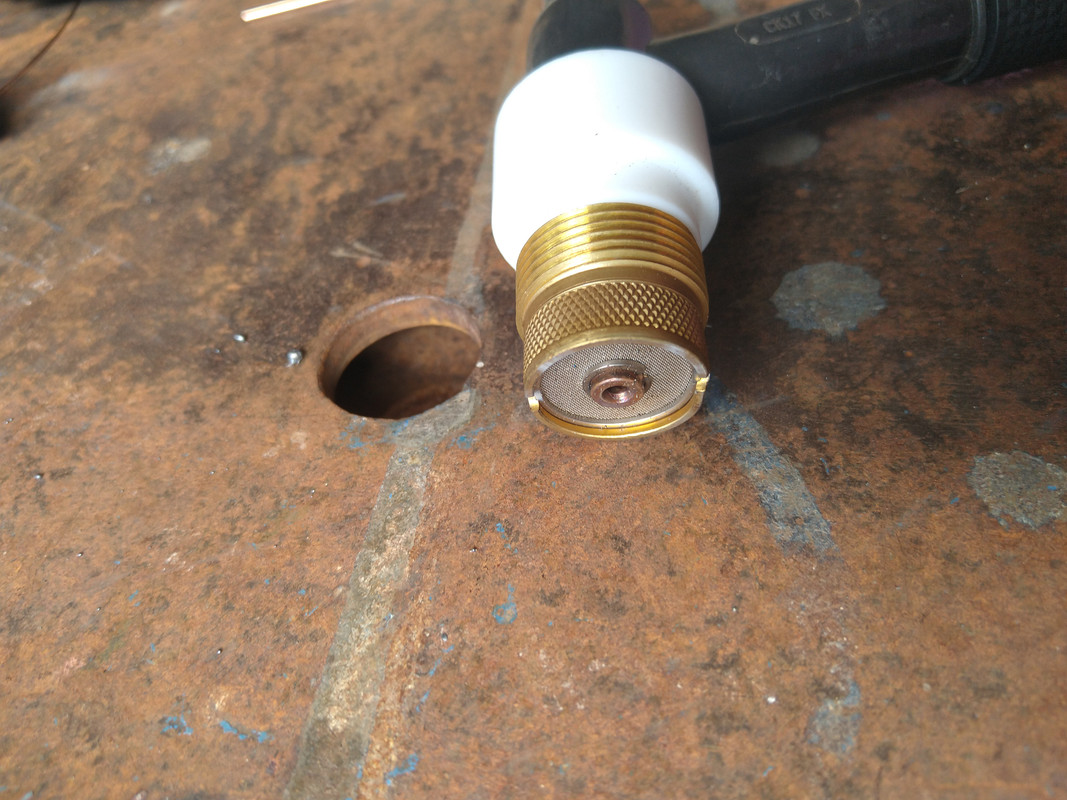
Here's the gas diffuser
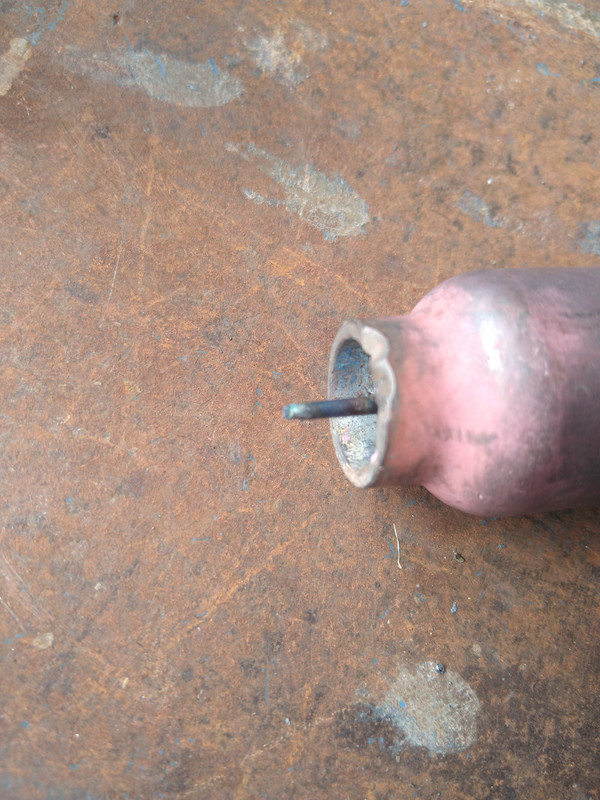
Here's the 3/32 tungsten stickout. The cup has seen better days, but is serviceable AFIAK
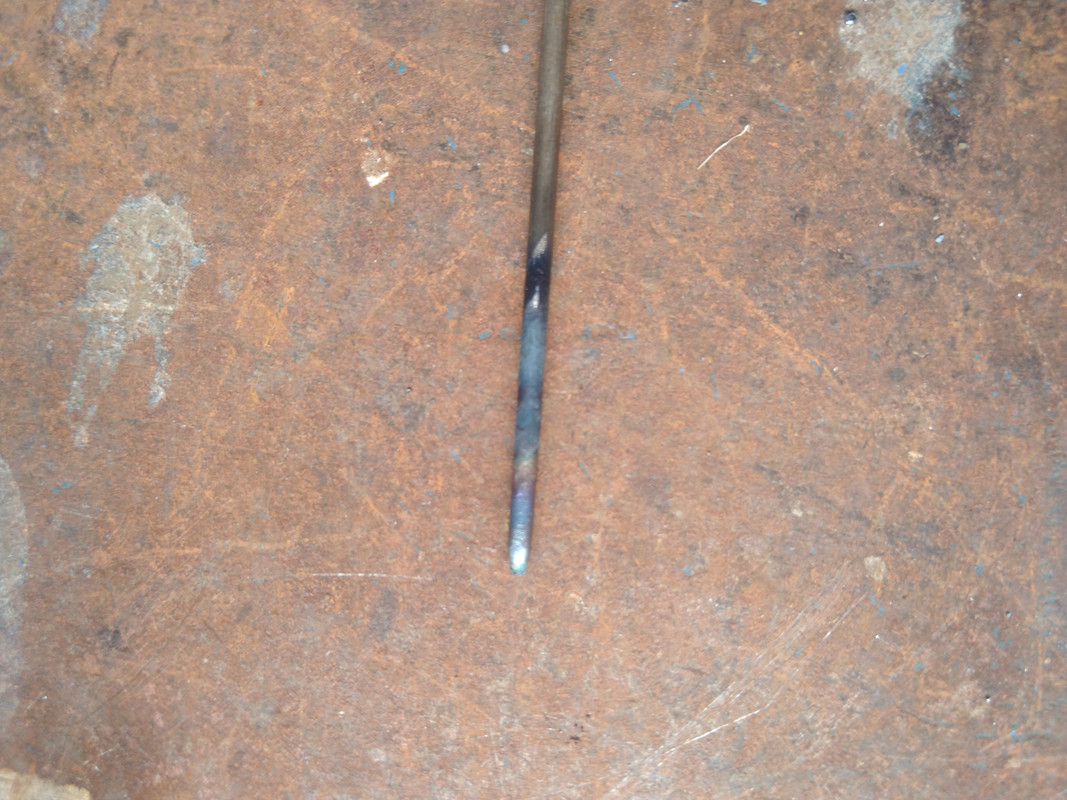
Here's the tungsten showing contamination.
I can understand contamination at the tip, but am surprised that there's contamination where it sits inside the diffuser. It builds up so that it is hard, but not too hard, to pull out for sharpening. I've made the mistake of removing some of that buildup on the grinder wheel used for sharpening. I see now that once that part becomes near the taper it'll cause problems, so won't do that anymore.
These pics are taken after welding for 5 minutes or so. Arc starts out alright, but then becomes unstable as contamination gets worse. Occasionally I'll get too close to the puddle or the filler, but don't recall that happening before these pictures. No matter what I do, I start getting a ball, or more really a flat mushroom on the tip. I'm starting out with a typical taper and a flat at the tip.
I weld in my garage, and get similar results whether the door is open or closed. I don't weld if I'm in a breeze.