Well just focusing on the amps/duty cycle business of things... I've been trying to do a little research... and I came across this video: https://www.youtube.com/watch?v=W8DV7lN7k9U
After 9:15 he joins some 25mm think rectangular stock. With foot to the floor at 220 amps he claims it was enough. Judging from the video, I guess his bead only penetrates as deep as it is fat... So I'm just guessing that the extra material doesn't make too much of a difference with sucking the heat out of the weld... which I suppose pre-heating would help.
so I'm guessing the absolute max thickness a 210 machine could weld would be 3/8" thick? Though I guess this is really pushing the limit. That seems like plenty of headroom for bike frames / swing arms. I guess the biggest connection points would be around the head stem and the swing arm pivot points, but I suppose if my box sections are only like 4mm at absolute max, then it should be a piece of cake, am I right?
Tig welding tips, questions, equipment, applications, instructions, techniques, tig welding machines, troubleshooting tig welding process
If the weldment is small, yes. I built these fence assemblies with a Syncrowave 250 and a Dynasty 300DX in tandem and the 250 amp cables/torch was not really enough. I would be better served in my industry with no less than a 350 amp machine and 300 amp torch/cables. 250 amps ends up being just enough for 6mm on most days if you want to make any money at it at all. Otherwise, you are going to be suffering trying to marry every trick in the book, along with the associated cheat hardware and consumables and extra time. Those plates on the bottom are 1/2". It took a LOT to get full penetration on those and god help you if you need to stop/restart. The one job pictured below, would have been worth spending another grand on the machine. I don't often weld things this big. It happens enough, though.KoroKoro wrote:Well just focusing on the amps/duty cycle business of things... I've been trying to do a little research... and I came across this video: https://www.youtube.com/watch?v=W8DV7lN7k9U
After 9:15 he joins some 25mm think rectangular stock. With foot to the floor at 220 amps he claims it was enough. Judging from the video, I guess his bead only penetrates as deep as it is fat... So I'm just guessing that the extra material doesn't make too much of a difference with sucking the heat out of the weld... which I suppose pre-heating would help.
so I'm guessing the absolute max thickness a 210 machine could weld would be 3/8" thick? Though I guess this is really pushing the limit. That seems like plenty of headroom for bike frames / swing arms. I guess the biggest connection points would be around the head stem and the swing arm pivot points, but I suppose if my box sections are only like 4mm at absolute max, then it should be a piece of cake, am I right?
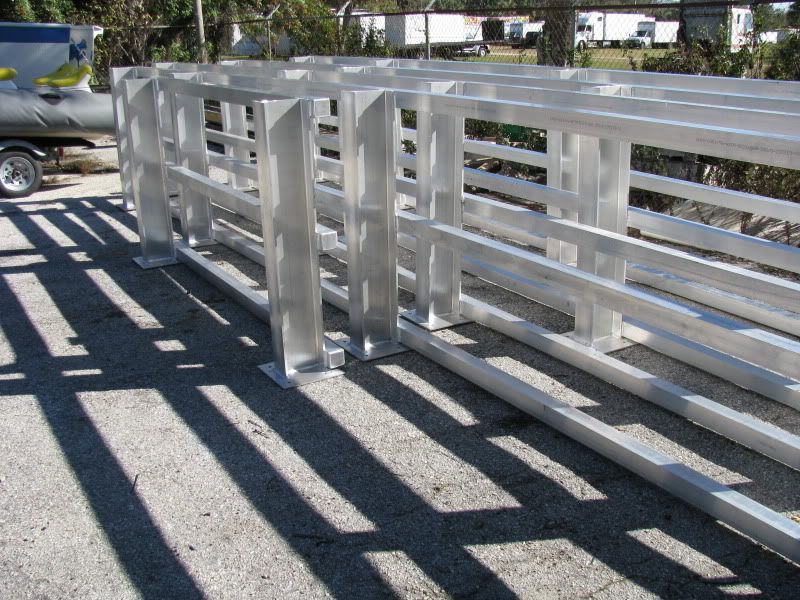
My welding buddies here locally all bought slightly underpowered machines in the 200 amp range. Whenever they get something larger in aluminum to weld, even if it's 12"x12" squares of 1/2" material to something, they come over to my house and ask to use my A/BP with very few settings, with it's CS410 torch and 300 amp cables. The upside being they refill my argon cylinder and leave me with rod and tungsten. I've threatened numerous times to just move my machine to our shop when we get larger projects in the photo because I will end up suffering through it for days at a time.
Then there's tacking. If you have ever or hope to ever weld in any kind of deadline, or production mode, slow tacking machines will eat your lunch in short order. I work by myself exclusively and don't always have time for elaborate fixtures or ability to hold awkward parts beyond that of a hope and a prayer. There has been times where I have had to put a clump of a weld on the base metal, hold the part with my other hand and heat it and the clump of tack as I position the part to within at least bashing range.
The budgets with buying welding equipment is typically within a few hundred, or a thousand dollars of the heavier duty version. Unless you are a company who specializes in a predictable type of material all the time, and may be buying 5-10 machines at a time, the savings is moot over the long haul, or even short term for that matter.
When a potential customer approaches you with something aluminum that is profitable, just by the sheer size of it, it's nice to be able to say, "Yes, I have the capability to weld that." That question gets asked a lot more than I realized it would when I bought my machine. I get a lot of work that other good welders simply do not have the power or time for or cannot do it economically without buying a bunch of extra stuff like helium.
I realize the benefits of knowing a lot of welding tips and tricks to eeek extra power and cheats out of lower powered machines just in case, but you really don't want to have to do it every day.
I know you have already stated what you intend to be welding and my input is a bit beyond that but almost every welder I know that has started out with a specified niche market, ended up being asked to do everything but.
Miller ABP 330, Syncrowave 250, Dynasty 300 DX.
Honorary member of the Fraternity of Faded Tee Shirts.
Honorary member of the Fraternity of Faded Tee Shirts.
I'd like to hear more about who you bought the Chinese welders from? When I bought my Everlast, I spoke to the company in the morning, flew to meet them shortly after noon, and surprised them when I walked in the door. I'm a try it before I buy it type of person, so I put it thru its paces, then placed my order. I fly for the cost of lunch, so I often hitchhike on the airlines, just for the heck of it. Having lifetime travel perks certainly comes in handy at times.
wrinkleneck wrote:Well, no offense, but I dug really deep this last two years and discovered that both Everlast and Longivity welders are extremely over-hyped where they spend HUGE money promoting their junk Chinese welders thru questionable west coast marketers, and also flood boards like this with false reviews..Plus their warranty and customer service sux. How do I know this?...From personal experience. I bought one of their welders last year and immediately my bank called to inform me that an hour after they debited my card for the welder, someone in India tried to debit me 1200 bucks for a meal at a restaurant, LOL. I got their junk welder and it blew up in my face first time I struck an arc....After attempting to return it under warranty, I gave up and tossed it local landfill. But that's just me and how it went for me. Buy whatever you want. Buy Chinese junk, or buy USA/European made and get stuff made to ISO standards.....Then attempt to get it fixed if it breaks
coldman
- coldman
Having a big powerful tig power source is great but the guy who might be considering a Chinese vs brandname machine is usually constrained by funds, power supply to their shed and the maximum thickness of metal they might be working on. In this case isn't a 200amp or smaller power source more appropriate?
I certainly won't be lugging a 350amp tig up onto a roof to weld pipework even though I drool at the sight of a Dynasty 350. Horses for courses.
Big jobs like your barrier fencing can be done with mig, if it was steel it would be migged, why not aly?
Cheers!
I certainly won't be lugging a 350amp tig up onto a roof to weld pipework even though I drool at the sight of a Dynasty 350. Horses for courses.
Big jobs like your barrier fencing can be done with mig, if it was steel it would be migged, why not aly?
Cheers!
I agree with TamJeff
welders and machines
one can make small things with big equipment
can't do big with small equipment
size matters
some is good,more is better,too much capabilities just about right
welders and machines
one can make small things with big equipment
can't do big with small equipment
size matters
some is good,more is better,too much capabilities just about right
Everlast 250EX
Miller 250 syncrowave
Sharp LMV Vertical Mill
Takisawa TSL-800-D Lathe
Coupla Bandsaws,Grinders,surface grinder,tool/cutter grinder
and more stuff than I deserve(Thanks Significant Other)
Miller 250 syncrowave
Sharp LMV Vertical Mill
Takisawa TSL-800-D Lathe
Coupla Bandsaws,Grinders,surface grinder,tool/cutter grinder
and more stuff than I deserve(Thanks Significant Other)
- TRACKRANGER
-
Weldmonger
-
Posts:
-
Joined:Wed Aug 06, 2014 12:48 am
-
Location:Melbourne, Australia
@TamJeff
Thanks for the great detail and explanations of benefits and shortcomings. You have shared some great insights.
But I wonder if MIG wouldn't have been a better choice for the fencing?
Thanks
Trevor
Thanks for the great detail and explanations of benefits and shortcomings. You have shared some great insights.
But I wonder if MIG wouldn't have been a better choice for the fencing?
Thanks
Trevor
EWM Phonenix 355 Pulse MIG set mainly for Aluminum, CIGWeld 300Amp AC/DC TIG, TRANSMIG S3C 300 Amp MIG, etc, etc
Yes, MIG would have been more practical but they wanted and paid extra for TIG welds. The fencing is one example. I also get a lot of rather large cast to weld as well and these swivel fuel depot fittings pictured below.
These take a lot of heat as well. Typically, I have a day to do them and on short notice.
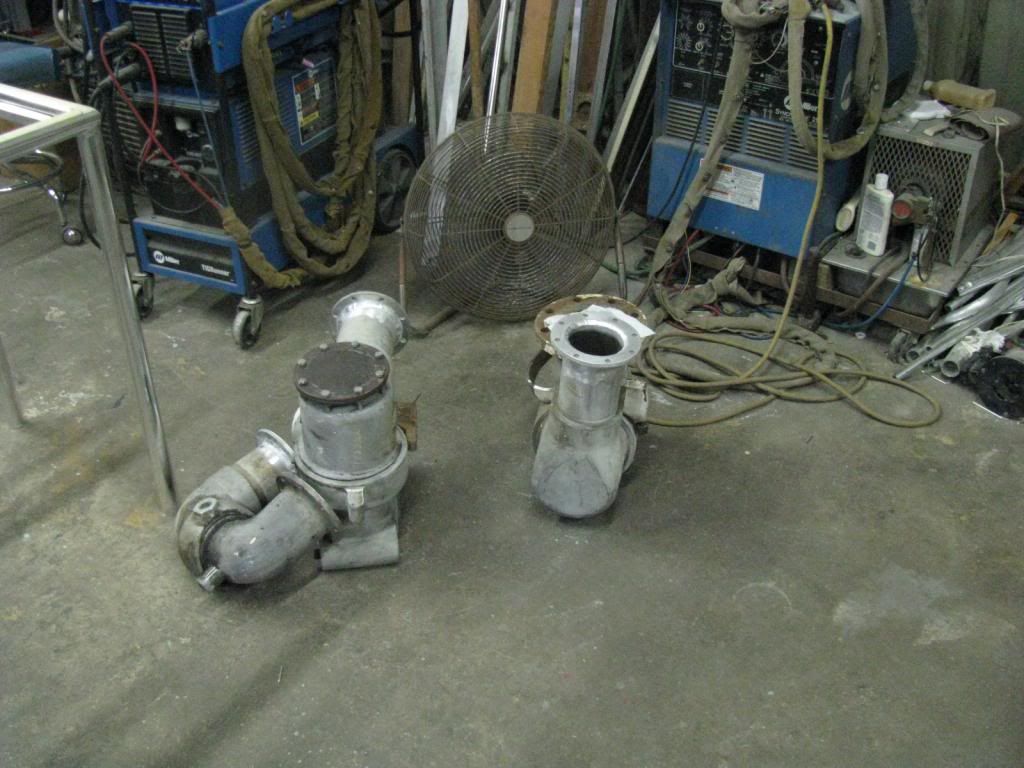
I get a lot of stuff like this where I wouldn't otherwise. Only takes a couple of these jobs to pay the difference in cost of welding machines. As far as a hobbyist, if the budget is limited, just save a little bit longer. Is pretty much how I do for most of my tools unless it's life or death emergency.
Not to say my way is the only way because I am essentially a hack so it's just a thought. Just been my observations over my years of TIG welding aluminum. Most people end up being 50 measly amps underpowered for what is considered typical, every day welding scenarios, not even considering industrial applications. Often times, I will find customers have been a few places before finding me, or I will have been recommended by another welder.
A larger machine may also run cooler running at half pace, and will likely extend the life of the machine as well, which may be why the older machines that were notoriously overbuilt are still around. I just find that when they generally claim a machine will weld a certain thickness of aluminum, it seems they have not considered the mass of what amounts to a huge heat sink once constructs start growing up, and out.
Our Dynasty 300DX I think weighs 90 lbs.
These take a lot of heat as well. Typically, I have a day to do them and on short notice.
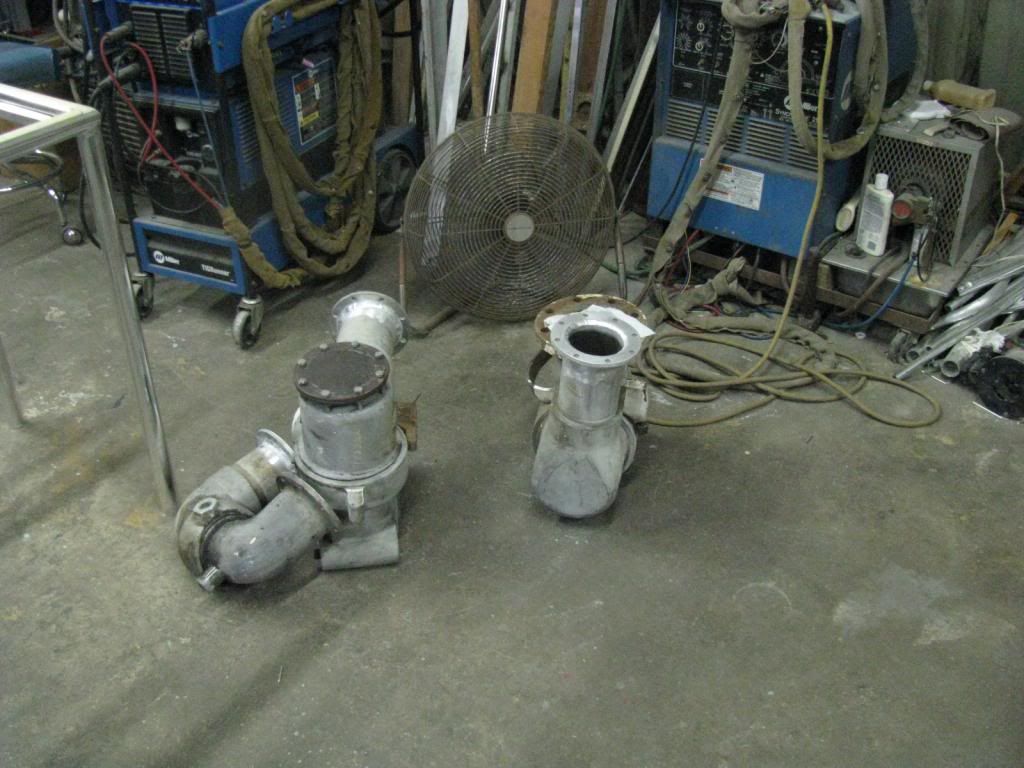
I get a lot of stuff like this where I wouldn't otherwise. Only takes a couple of these jobs to pay the difference in cost of welding machines. As far as a hobbyist, if the budget is limited, just save a little bit longer. Is pretty much how I do for most of my tools unless it's life or death emergency.
Not to say my way is the only way because I am essentially a hack so it's just a thought. Just been my observations over my years of TIG welding aluminum. Most people end up being 50 measly amps underpowered for what is considered typical, every day welding scenarios, not even considering industrial applications. Often times, I will find customers have been a few places before finding me, or I will have been recommended by another welder.
A larger machine may also run cooler running at half pace, and will likely extend the life of the machine as well, which may be why the older machines that were notoriously overbuilt are still around. I just find that when they generally claim a machine will weld a certain thickness of aluminum, it seems they have not considered the mass of what amounts to a huge heat sink once constructs start growing up, and out.
Our Dynasty 300DX I think weighs 90 lbs.
Miller ABP 330, Syncrowave 250, Dynasty 300 DX.
Honorary member of the Fraternity of Faded Tee Shirts.
Honorary member of the Fraternity of Faded Tee Shirts.
My first was 250 Dial Arc HF
Then 250 Syncrowave
added to it a Everlast 250EX for all features most of my welding is under 1/8 alum/steel headers and such with CK flex lock series 2 air cooled. Handy
When I need to really weld go to the syncrowave and when I really,really need to weld go to friends APB. Wish I had room I would have one. Around here they go for $400-$1000. No room for one
per TamJeff
Size matters
Then 250 Syncrowave
added to it a Everlast 250EX for all features most of my welding is under 1/8 alum/steel headers and such with CK flex lock series 2 air cooled. Handy
When I need to really weld go to the syncrowave and when I really,really need to weld go to friends APB. Wish I had room I would have one. Around here they go for $400-$1000. No room for one
per TamJeff
Size matters
Everlast 250EX
Miller 250 syncrowave
Sharp LMV Vertical Mill
Takisawa TSL-800-D Lathe
Coupla Bandsaws,Grinders,surface grinder,tool/cutter grinder
and more stuff than I deserve(Thanks Significant Other)
Miller 250 syncrowave
Sharp LMV Vertical Mill
Takisawa TSL-800-D Lathe
Coupla Bandsaws,Grinders,surface grinder,tool/cutter grinder
and more stuff than I deserve(Thanks Significant Other)
- TRACKRANGER
-
Weldmonger
-
Posts:
-
Joined:Wed Aug 06, 2014 12:48 am
-
Location:Melbourne, Australia
@TamJeff
Thanks for the clarification on the TIG vs MIG.
I've got a CIG TRANSMIG 300Amp setup for steel. Older Transformer job. It's absolutely bullet-proof.
I have a German manufactured EWM Phoenix 355 MIG which will run 350 Amps, and setup purely for Aluminum
and a TRANSTIG 300A AC/DC TIG which I mainly use for Stainless and Aluminum
I haven't reached a limit yet, but I sure have worked the TRANSTIG hard at times on Aluminum.
BTW: You sure get up to some tricks!
Thanks
Trevor
Thanks for the clarification on the TIG vs MIG.
I've got a CIG TRANSMIG 300Amp setup for steel. Older Transformer job. It's absolutely bullet-proof.
I have a German manufactured EWM Phoenix 355 MIG which will run 350 Amps, and setup purely for Aluminum
and a TRANSTIG 300A AC/DC TIG which I mainly use for Stainless and Aluminum
I haven't reached a limit yet, but I sure have worked the TRANSTIG hard at times on Aluminum.
BTW: You sure get up to some tricks!
Thanks
Trevor
EWM Phonenix 355 Pulse MIG set mainly for Aluminum, CIGWeld 300Amp AC/DC TIG, TRANSMIG S3C 300 Amp MIG, etc, etc
coldman
- coldman
@Tamjeff
I hear you man and agree with what you say but there are exceptions. You talk about paid jobs covering the cost of bigger better machines, ok.
What if you go to night school trying to add a string to your bow while raising a family and paying alimony and your teacher says you need to practice at home now not when you can save up for blue, what are you going to do?
And how many home garages or sheds can power up a 350amp machine with 3-phase?
What if you just want a machine to fabricate your own fancy front gate to your new house and you know the machine will be idle after that until you get around to restoring that 1946 chevy out the back?
There will always be a need and market for these "entry level" machines. People and businesses that rely on welding for a crust should have professional quality machines with more than enough grunt to complete their work or they are fooling themselves.
Most pipe welders I work with use good machines like Esab and Kempi, but they are all 160amp dc scratch start tig/stick power sources because they are light and won't trip 15amp single phase circuits. They would like more grunt for running bigger rods but aren't willing to go to heavier units to lug up ladders and around roof spaces. Some have suggested I might be a fancy pants from Melbourne because I use a Dynasty 200DX, but its twice the weight of their machines and don't I know it when I have to go three flights of stairs, a ladder and 150m across a roof to get to where I need to be. And I run it on 3-phase so I don't trip breakers on 15amp single phase circuits on sites. In my shop I have 3 phase and 30amp single phase, I can run what I like. If I can't handle jobs with my 200DX I switch on my 300amp CIG transmig. I can't use these machines at home, but I'm lucky - I don't need to. So I can understand people considering non-brand and/or underpowered machines when entering the market.
Just my two cents worth anyway.
I hear you man and agree with what you say but there are exceptions. You talk about paid jobs covering the cost of bigger better machines, ok.
What if you go to night school trying to add a string to your bow while raising a family and paying alimony and your teacher says you need to practice at home now not when you can save up for blue, what are you going to do?
And how many home garages or sheds can power up a 350amp machine with 3-phase?
What if you just want a machine to fabricate your own fancy front gate to your new house and you know the machine will be idle after that until you get around to restoring that 1946 chevy out the back?
There will always be a need and market for these "entry level" machines. People and businesses that rely on welding for a crust should have professional quality machines with more than enough grunt to complete their work or they are fooling themselves.
Most pipe welders I work with use good machines like Esab and Kempi, but they are all 160amp dc scratch start tig/stick power sources because they are light and won't trip 15amp single phase circuits. They would like more grunt for running bigger rods but aren't willing to go to heavier units to lug up ladders and around roof spaces. Some have suggested I might be a fancy pants from Melbourne because I use a Dynasty 200DX, but its twice the weight of their machines and don't I know it when I have to go three flights of stairs, a ladder and 150m across a roof to get to where I need to be. And I run it on 3-phase so I don't trip breakers on 15amp single phase circuits on sites. In my shop I have 3 phase and 30amp single phase, I can run what I like. If I can't handle jobs with my 200DX I switch on my 300amp CIG transmig. I can't use these machines at home, but I'm lucky - I don't need to. So I can understand people considering non-brand and/or underpowered machines when entering the market.
Just my two cents worth anyway.
wrinkleneck wrote:Please consider the HTP-221 Invertig from HTP America at USAWELD.COM
My HTP-221 arrives Monday...The HTP-221 replaced the old HTP-201 several years ago and you won't find the FIRST negative comment about it anywhere on the web. They produced the older 201 for over ten years and many are still being used all over the world today....And BTW, HTP products are made in Italy, no China.
I think what you will like most about the HTP-221 is it actually has every possible feature....HF start, slope up, slope down, pre gas, post gas, AC balance, high speed pulse, AC freq, starting amps, final amps...EVERYTHING is adjustable and puts you in total control where once you dial in the perfect settings, you can save it and 63 other weld settings.
Do you need to TIG a dirty alum casting, then the HTP is your choice. Do you want stick weld AC/DC with total control of AC freq, then again, the HTP is the one....Do you want to TIG any position and have full control of penetration yet a puddle that clings even overhead, the the pulse feature on the HTP will get you there instantly.
It also comes with hi quality 17 series torch, decent foot pedal and argon regulator and hose for $2495..You add add a very high quality water cooler and torch for a little more money.
Compare the HTP-221 to the Miller Dynasty 200 and you will see you get lots more welder for many less bucks and a fantastic warranty and customer service.
Good luck, and congrats no matter which you buy
I agree completely. You also get independent amplitude control in AC mode which you cannot find in any welder in it's class/price range. I've had my 221 since last December and love it. The dual-voltage model actually puts out 225-230A, eve if it is not rated as such. With a 20% duty cycle @ 220A, it's a pretty good work horse. Add a water cooled torch setup and you have one killer welding rig.
Believe it or not, the owner of HTP makes sure their employees don't spam advertisements. It was either here or in another welding forum where a while back Jeff, the owner, actually posted regarding this when someone who posted was believed to be an HTP employee. He quickly got the record straight.
Ditto. I spent a lot of time hanging out on Everlast's forum watching the good and bad, and their reaction to it. Watching threads in real-time ensures that the negative press isn't being deleted, and I never saw that happen. Generally, what I saw was that crap happens, they dealt with it as I'd expect, particularly on a faulty new unit. On theater hand, I saw that repair jobs took months, so plan accordingly.WerkSpace wrote:I'd like to hear more about who you bought the Chinese welders from? When I bought my Everlast, I spoke to the company in the morning, flew to meet them shortly after noon, and surprised them when I walked in the door. I'm a try it before I buy it type of person, so I put it thru its paces, then placed my order. I fly for the cost of lunch, so I often hitchhike on the airlines, just for the heck of it. Having lifetime travel perks certainly comes in handy at times.
Airline benefits... Industry retiree? I was single at an airline in the deregulation heyday of the late 80's. Low load factors, easy non-rev... those were some really good times! It'd be amazing to have that retirement benefit, but the pay elsewhere was way better.
As a point of interest for the OP, Everlast's 325-Amp welder is now available in single-phase 220v/60A at the same duty cycle, though I don't think the website is updated yet. That's the one in my crosshairs.
http://www.everlastgenerators.com/forum ... e-480V-too
Cheers,
Richard
Grinding discs... still my #1 consumable!
Return to “Tig Welding - Tig Welding Aluminum - Tig Welding Techniques - Aluminum Tig Welding”
Jump to
- Introductions & How to Use the Forum
- ↳ Welcome!
- ↳ Member Introductions
- ↳ How to Use the Forum
- ↳ Moderator Applications
- Welding Discussion
- ↳ Metal Cutting
- ↳ Tig Welding - Tig Welding Aluminum - Tig Welding Techniques - Aluminum Tig Welding
- ↳ Mig and Flux Core - gas metal arc welding & flux cored arc welding
- ↳ Stick Welding/Arc Welding - Shielded Metal Arc Welding
- ↳ Welding Forum General Shop Talk
- ↳ Welding Certification - Stick/Arc Welding, Tig Welding, Mig Welding Certification tests - Welding Tests of all kinds
- ↳ Welding Projects - Welding project Ideas - Welding project plans
- ↳ Product Reviews
- ↳ Fuel Gas Heating
- Welding Tips & Tricks
- ↳ Video Discussion
- ↳ Wish List
- Announcements & Feedback
- ↳ Forum News
- ↳ Suggestions, Feedback and Support
- Welding Marketplace
- ↳ Welding Jobs - Industrial Welding Jobs - Pipe Welding Jobs - Tig Welding Jobs
- ↳ Classifieds - Buy, Sell, Trade Used Welding Equipment
- Welding Resources
- ↳ Tradeshows, Seminars and Events
- ↳ The Welding Library
- ↳ Education Opportunities