This is a picture of a root pass I made with the intent to make two more, how do i eliminate the "undercut" on the top of the weld?
This weld was made with a Millermatic 252 using dual shield 0.35 wire
mig and flux core tips and techniques, equipment, filler metal
- weldin mike 27
-
Weldmonger
-
Posts:
-
Joined:Fri Apr 01, 2011 10:59 pm
-
Location:Australia; Victoria
Hey,
I find that is caused by driving the wire right into the corner of the joint. Pull the arc back about 2-3mm out onto the bottom plate and let the weld wash across on to the vertical piece. Also, lower your gun angle toward the bottom plate so the weld metal is forced upwards onto the vertical piece.
Mick
I find that is caused by driving the wire right into the corner of the joint. Pull the arc back about 2-3mm out onto the bottom plate and let the weld wash across on to the vertical piece. Also, lower your gun angle toward the bottom plate so the weld metal is forced upwards onto the vertical piece.
Mick
Thanks for the input, what your saying makes sense ill give that a shot. This is a shot of some of my second and third pass's. I have very little experience with multipass welding, how do i get rid of that ledge from pass two to pass three?
- Attachments
-
- download_20141206_160643.jpeg (48.3 KiB) Viewed 1551 times
jwright650
- jwright650
-
Ace
-
Posts:
-
Joined:Wed Dec 03, 2014 3:27 pm
To me it looks like your voltage may be too high due to the pot marks(gas tracks) on the cap. But the overlap is probably travel speed is a bit slow for the small wire and it's piling up and rolling over. Hard to tell from the pic, but how wide is the cap on that top pass that is starting to overlap?
John Wright
AWS Certified Welding Inspector
NDT Level II UT, VT, MT and PT
NACE CIP Level I Coating Inspector
AWS Certified Welding Inspector
NDT Level II UT, VT, MT and PT
NACE CIP Level I Coating Inspector
cap pass is around 1/2". What are the pot marks? I'm new to the lingo. I will try and speed up my travel and see if that helps. The Miller I'm using and I'm sure most due have there recommended or starting points for voltage and wire speed. So are these starting points good for both dual and self shield?jwright650 wrote:To me it looks like your voltage may be too high due to the pot marks(gas tracks) on the cap. But the overlap is probably travel speed is a bit slow for the small wire and it's piling up and rolling over. Hard to tell from the pic, but how wide is the cap on that top pass that is starting to overlap?
- AKweldshop
-
Weldmonger
-
Posts:
-
Joined:Wed Oct 23, 2013 3:30 pm
-
Location:Palmer AK
Hard for me to diagnose that bead.
Hard to imagine using .035 wire on such thick metal.
I'd at least be using .045.....
I wish I could link you a good duelshield video to watch, but there is none....
Hard to imagine using .035 wire on such thick metal.
I'd at least be using .045.....
I wish I could link you a good duelshield video to watch, but there is none....

- IMG_1020.JPG (61.89 KiB) Viewed 1527 times
Just a couple welders and a couple of big hammers and torches.
Men in dirty jeans built this country, while men in clean suits have destroyed it.
Trump/Carson 2016-2024
Men in dirty jeans built this country, while men in clean suits have destroyed it.
Trump/Carson 2016-2024
- AKweldshop
-
Weldmonger
-
Posts:
-
Joined:Wed Oct 23, 2013 3:30 pm
-
Location:Palmer AK
- IMG_0533.JPG (75.35 KiB) Viewed 1523 times
Just a couple welders and a couple of big hammers and torches.
Men in dirty jeans built this country, while men in clean suits have destroyed it.
Trump/Carson 2016-2024
Men in dirty jeans built this country, while men in clean suits have destroyed it.
Trump/Carson 2016-2024
Nice work. Thats what I'm looking for. thanks for the post. i also think I need to start using .045. I didn't mention it before but I am using 92/8 because thats what we had. When I asked about it I was told thats just what we use here. I did talk my boss into getting a tank of c25. Could that be part of my uppercut/ voltage problem?
- Superiorwelding
-
Weldmonger
-
Posts:
-
Joined:Thu Jan 24, 2013 10:13 pm
-
Location:Eddy, TX
AKweldshop,
Make us a video!!
-Jonathan
Make us a video!!
-Jonathan
Instagram- @superiorwelding/@learntotig
Twitter- @_JonathanLewis
https://www.learntotig.com
https://www.superiorweldandfab.com
https://www.youtube.com/+SuperiorWeldin ... ATHANLEWIS
Twitter- @_JonathanLewis
https://www.learntotig.com
https://www.superiorweldandfab.com
https://www.youtube.com/+SuperiorWeldin ... ATHANLEWIS
- AKweldshop
-
Weldmonger
-
Posts:
-
Joined:Wed Oct 23, 2013 3:30 pm
-
Location:Palmer AK
Superiorwelding wrote:AKweldshop,
Make us a video!!
-Jonathan
Superiorwelding,
I'd rather post pics.
Video's greatly diminish in applicable value without arc shots.
This is 3/8" steel to 1/2" steel/
Hobart .045 wire.
The pics above are Esab .045 wire.
- IMG_0053.JPG (84.96 KiB) Viewed 1088 times
- IMG_0052.JPG (57.96 KiB) Viewed 1088 times
Just a couple welders and a couple of big hammers and torches.
Men in dirty jeans built this country, while men in clean suits have destroyed it.
Trump/Carson 2016-2024
Men in dirty jeans built this country, while men in clean suits have destroyed it.
Trump/Carson 2016-2024
- Superiorwelding
-
Weldmonger
-
Posts:
-
Joined:Thu Jan 24, 2013 10:13 pm
-
Location:Eddy, TX
John,
Come on, be a good sport.
-Jonathan
Come on, be a good sport.

-Jonathan
Instagram- @superiorwelding/@learntotig
Twitter- @_JonathanLewis
https://www.learntotig.com
https://www.superiorweldandfab.com
https://www.youtube.com/+SuperiorWeldin ... ATHANLEWIS
Twitter- @_JonathanLewis
https://www.learntotig.com
https://www.superiorweldandfab.com
https://www.youtube.com/+SuperiorWeldin ... ATHANLEWIS
- AKweldshop
-
Weldmonger
-
Posts:
-
Joined:Wed Oct 23, 2013 3:30 pm
-
Location:Palmer AK
bigworm40 wrote:Nice work. Thats what I'm looking for. thanks for the post. i also think I need to start using .045. I didn't mention it before but I am using 92/8 because thats what we had. When I asked about it I was told thats just what we use here. I did talk my boss into getting a tank of c25. Could that be part of my uppercut/ voltage problem?
I can't speak to 92/8, as I've never used any of it for duelshield wire.
I've used Hobart 80 something, Esab 71x, and Lincoln 71m, all with 75/25 Ar/Co2. All .045 dia.
The perform just fine for me.
Co2 is supposed to work as well. I just use 75/25 because that's what I have.
Just a couple welders and a couple of big hammers and torches.
Men in dirty jeans built this country, while men in clean suits have destroyed it.
Trump/Carson 2016-2024
Men in dirty jeans built this country, while men in clean suits have destroyed it.
Trump/Carson 2016-2024
- AKweldshop
-
Weldmonger
-
Posts:
-
Joined:Wed Oct 23, 2013 3:30 pm
-
Location:Palmer AK
Superiorwelding wrote:John,
Come on, be a good sport.![]()
-Jonathan
The problem with being a good sport, is that I have to loose to prove it.

Just a couple welders and a couple of big hammers and torches.
Men in dirty jeans built this country, while men in clean suits have destroyed it.
Trump/Carson 2016-2024
Men in dirty jeans built this country, while men in clean suits have destroyed it.
Trump/Carson 2016-2024
- weldin mike 27
-
Weldmonger
-
Posts:
-
Joined:Fri Apr 01, 2011 10:59 pm
-
Location:Australia; Victoria
With small wire, you can't just go slower and have it match the bigger stuff. To make a 3/8 fillet with .035 you may need 4 runs. Set the machine to your known settings and travel fast enough to keep the arc on the front edge of the puddle, if this results in a small weld, lay more beads, in the same pattern. The undercut comes from slow travel speed and letting the pool become too big for the available wire.
Mick
Mick
Thanks gus for all your advice. I did talk my boss into picking up a spool or .045 wire. Does anyone know anything about http://www.lincolnelectric.com/en-us/Co ... nElectric)
Our local supply store stocks this wire. They also ordered me the drive roller kit and the gun sleeve. If you have any experience with this wire let me know.
The picture below is of the project I'm working on. All the material is A572 grade 50 1/2" except the hubbs. Its's 48"s long and I have it laid out to run 4" stitch welds all the way around. Would that be the correct method of welding to use or should i just run fillet welds as long as comfortably possible?
Our local supply store stocks this wire. They also ordered me the drive roller kit and the gun sleeve. If you have any experience with this wire let me know.
The picture below is of the project I'm working on. All the material is A572 grade 50 1/2" except the hubbs. Its's 48"s long and I have it laid out to run 4" stitch welds all the way around. Would that be the correct method of welding to use or should i just run fillet welds as long as comfortably possible?
- Attachments
-
- 20141208_151805.jpg (53.15 KiB) Viewed 1065 times
jwright650
- jwright650
-
Ace
-
Posts:
-
Joined:Wed Dec 03, 2014 3:27 pm
The shop I was in was always worried about the cost of supplies, so CO2 was the shielding of choice due to it being cheaper than the argon mixes. It works well with 1/16" ESAB E71T-1 and the like. That small diameter wire (.035) has to really pile up to run passes as large as the OP is posting about. I would be concerned about running stringers that large and maintaining good penetration to the root. The arc can get kind of lazy if you are not out on the leading edge so it can dig in and cut out the root as you go. For structural steel fabrication, most shops that I've been in and inspected in were running .045 as their all around wire, and larger dia. FCAW wires for the heavier work.
Here is a pic(pic quality not so good) of stringers run in a full pen joint with 3/32" dia. Hobart E70T-1 with CO2 shielding.
450a/29.5v travelling around 12-15 ipm with 1" stickout
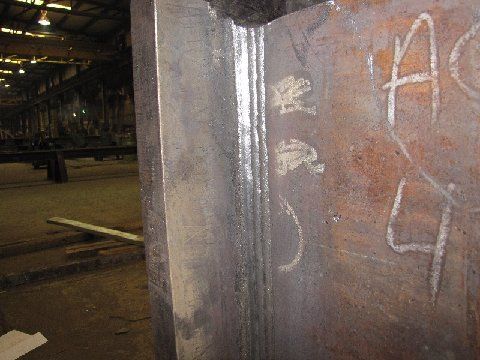
Here is a pdf from ESAB about their .035 wire....try the recommended parameters and see how they work for you, in the past I found they work just fine on the upper end of the ranges for higher deposition rates.
http://mam.esab.com/assets/1/BDBA5CC688 ... ain-01.pdf
Here is a pic(pic quality not so good) of stringers run in a full pen joint with 3/32" dia. Hobart E70T-1 with CO2 shielding.
450a/29.5v travelling around 12-15 ipm with 1" stickout
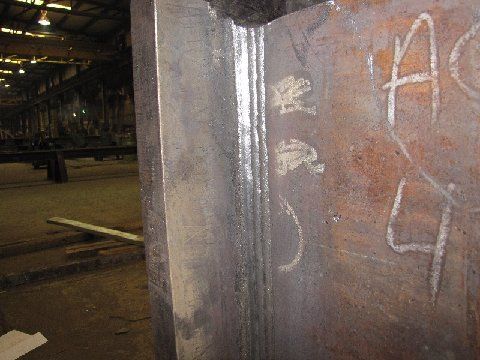
Here is a pdf from ESAB about their .035 wire....try the recommended parameters and see how they work for you, in the past I found they work just fine on the upper end of the ranges for higher deposition rates.
http://mam.esab.com/assets/1/BDBA5CC688 ... ain-01.pdf
John Wright
AWS Certified Welding Inspector
NDT Level II UT, VT, MT and PT
NACE CIP Level I Coating Inspector
AWS Certified Welding Inspector
NDT Level II UT, VT, MT and PT
NACE CIP Level I Coating Inspector
Thanks for all your input John and everyone else. You guys are helping me out greatly. Could some one please explain what causes these tracks in the weld.
- Attachments
-
- 1418141101204-1979449497.jpg (52.87 KiB) Viewed 1056 times
jwright650
- jwright650
-
Ace
-
Posts:
-
Joined:Wed Dec 03, 2014 3:27 pm
I have found that the voltage set a bit too high for faster travel speeds led to an increase of seeing those(worm tracks) on the cap/under the slag. I think the slag freezes due to the fast travel speeds and doesn't give the gas time enough to escape(<-my theory).bigworm40 wrote:Thanks for all your input John and everyone else. You guys are helping me out greatly. Could some one please explain what causes these tracks in the weld.
John Wright
AWS Certified Welding Inspector
NDT Level II UT, VT, MT and PT
NACE CIP Level I Coating Inspector
AWS Certified Welding Inspector
NDT Level II UT, VT, MT and PT
NACE CIP Level I Coating Inspector
- Superiorwelding
-
Weldmonger
-
Posts:
-
Joined:Thu Jan 24, 2013 10:13 pm
-
Location:Eddy, TX
To complement Mr. Wright's statement it is likely your gas flow is to high. I posted a article to back this up a long time ago and will try to look it back up and post it here. What is your CFH?
-Jonathan
-Jonathan
Instagram- @superiorwelding/@learntotig
Twitter- @_JonathanLewis
https://www.learntotig.com
https://www.superiorweldandfab.com
https://www.youtube.com/+SuperiorWeldin ... ATHANLEWIS
Twitter- @_JonathanLewis
https://www.learntotig.com
https://www.superiorweldandfab.com
https://www.youtube.com/+SuperiorWeldin ... ATHANLEWIS
jwright650
- jwright650
-
Ace
-
Posts:
-
Joined:Wed Dec 03, 2014 3:27 pm
That gas flow sounds good to me, I wrote my WPSs for the (1/16" and 3/32")FCAW that we used at 40-45cfh and generally didn't have any coverage issues unless a OH door was opened or a shop fan accidentally turned in the direction of the welding.bigworm40 wrote:40
John Wright
AWS Certified Welding Inspector
NDT Level II UT, VT, MT and PT
NACE CIP Level I Coating Inspector
AWS Certified Welding Inspector
NDT Level II UT, VT, MT and PT
NACE CIP Level I Coating Inspector
jwright650
- jwright650
-
Ace
-
Posts:
-
Joined:Wed Dec 03, 2014 3:27 pm
I had a kid in our shop who thought a little gas is good so a lot must be better...LOL I think when the gas flow is too strong it creates a vortex or you get "eddies" that suck in atmosphere when approaching an inside corner.Superiorwelding wrote:To complement Mr. Wright's statement it is likely your gas flow is to high. I posted a article to back this up a long time ago and will try to look it back up and post it here. What is your CFH?
-Jonathan
ie welding inside the web of a column at a base plate (base plate to column shaft)
John Wright
AWS Certified Welding Inspector
NDT Level II UT, VT, MT and PT
NACE CIP Level I Coating Inspector
AWS Certified Welding Inspector
NDT Level II UT, VT, MT and PT
NACE CIP Level I Coating Inspector
Return to “Mig and Flux Core - gas metal arc welding & flux cored arc welding”
Jump to
- Introductions & How to Use the Forum
- ↳ Welcome!
- ↳ Member Introductions
- ↳ How to Use the Forum
- ↳ Moderator Applications
- Welding Discussion
- ↳ Metal Cutting
- ↳ Tig Welding - Tig Welding Aluminum - Tig Welding Techniques - Aluminum Tig Welding
- ↳ Mig and Flux Core - gas metal arc welding & flux cored arc welding
- ↳ Stick Welding/Arc Welding - Shielded Metal Arc Welding
- ↳ Welding Forum General Shop Talk
- ↳ Welding Certification - Stick/Arc Welding, Tig Welding, Mig Welding Certification tests - Welding Tests of all kinds
- ↳ Welding Projects - Welding project Ideas - Welding project plans
- ↳ Product Reviews
- ↳ Fuel Gas Heating
- Welding Tips & Tricks
- ↳ Video Discussion
- ↳ Wish List
- Announcements & Feedback
- ↳ Forum News
- ↳ Suggestions, Feedback and Support
- Welding Marketplace
- ↳ Welding Jobs - Industrial Welding Jobs - Pipe Welding Jobs - Tig Welding Jobs
- ↳ Classifieds - Buy, Sell, Trade Used Welding Equipment
- Welding Resources
- ↳ Tradeshows, Seminars and Events
- ↳ The Welding Library
- ↳ Education Opportunities