Folks, here is my complete review of the Eastwood TIG 200 AC/DC
http://youtu.be/rTfc62WNvn4?list=UUJWQm ... aTma2q31Qg
Tig welding tips, questions, equipment, applications, instructions, techniques, tig welding machines, troubleshooting tig welding process
Check out my journey through welding school https://www.youtube.com/channel/UCJWQmJ ... aTma2q31Qg
Glad you like the machine. Two corrections though. Tig Torch = not top of the line. T.O.T.L is generally accepted to be: Weldtec/Tec Torch, CK Worldwide, Weldcraft. That is not a superflex cable. It is a sheathed cheap rubber that will deteriorate, especially if you do any AC welding. Once you actually own a Superflex cable, you immediately know the difference. Want real T.O.T.L, order the CK torch/superflex cable package that HTP America sells on their Ebay store. You will immediately hate yourself for even contemplating that the Eastwood stuff was T.O.T.L.
The machine, however, does have plenty of balls. It can easily do it's rated power and cook your hose from the tig torch end if you're not careful. I know mine did. 
With the proper TIG torch and cable, possibly even adapted to a water-cooled setup, would make an excellent TIG welder setup that most any hobbyist would unlikely outgrow.
Oh, and the audio needs work. Sounds low and muffled.


With the proper TIG torch and cable, possibly even adapted to a water-cooled setup, would make an excellent TIG welder setup that most any hobbyist would unlikely outgrow.
Oh, and the audio needs work. Sounds low and muffled.

jwright650
- jwright650
-
Ace
-
Posts:
-
Joined:Wed Dec 03, 2014 3:27 pm
I have one of those...I was disappointed that I couldn't stick weld with it...well, it didn't have a connection on the front of the machine for a stick electrode holder/lead to hook up. The electrical connections are a bit cheap too, the plastic is fragile and needs lots of care when setting up and putting it away. But for the money, I like the machine and it does Tig fairly well for my needs. Be careful on really thin materials, it doesn't have any way that I know of to reduce the startup amps and it can blow right through even when set way down low. To get around that startup issue, I lay the filler in close and strike off on that first then move over to the thin material.
John Wright
AWS Certified Welding Inspector
NDT Level II UT, VT, MT and PT
NACE CIP Level I Coating Inspector
AWS Certified Welding Inspector
NDT Level II UT, VT, MT and PT
NACE CIP Level I Coating Inspector
Thanks for the input guys. I was unaware of the cable not being a Superflex. As for the torch, a have a CK17F on my other unit and I don't notice any real difference. My biggest beef with the Eastwood is the arc cutoff in AC. When I try to taper off it cuts out way too soon. On DC it doesn't have this problem.
Check out my journey through welding school https://www.youtube.com/channel/UCJWQmJ ... aTma2q31Qg
Don't get me wrong, the cable is very flexible, but a true super flex is even more flexible and about half the weight.
Also, this is what happens if you're not careful on AC welding:
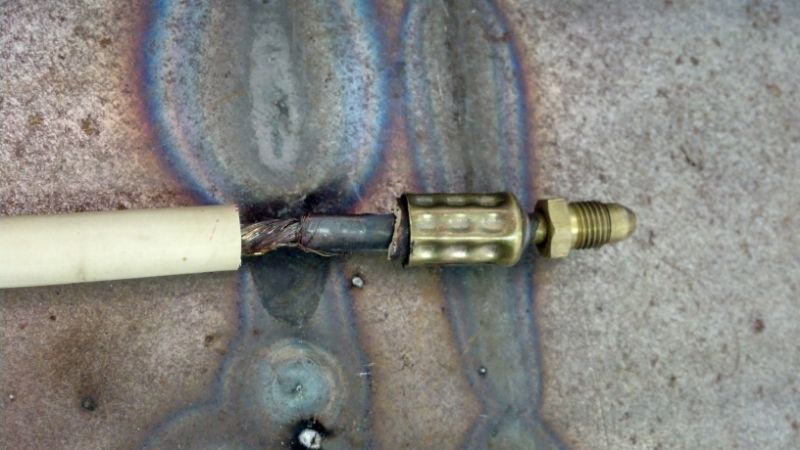
That is the torch end. The "missing" part I had already chopped off because it was cooked from the heat in the torch that inevitably makes its way down to the fitting/cable junction during the course of AC welding where there is much more heat into the tig torch. That maroon sheath? Nowhere to be found as it had shriveled up and melted back, exposing the actual hose.
Also, this is what happens if you're not careful on AC welding:
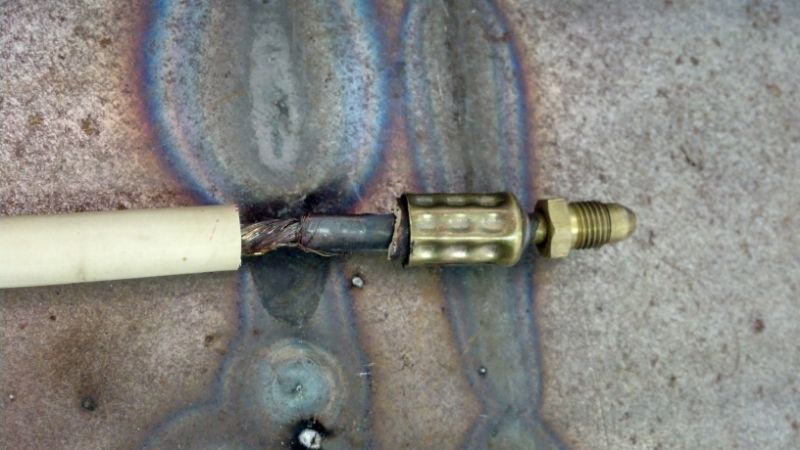
That is the torch end. The "missing" part I had already chopped off because it was cooked from the heat in the torch that inevitably makes its way down to the fitting/cable junction during the course of AC welding where there is much more heat into the tig torch. That maroon sheath? Nowhere to be found as it had shriveled up and melted back, exposing the actual hose.
jwright650
- jwright650
-
Ace
-
Posts:
-
Joined:Wed Dec 03, 2014 3:27 pm
I wondered how that gas hose carried 200 amps of current...apparently it doesn't always...I will have to be careful wrapping all of that up when putting the welder away after I use it.
John Wright
AWS Certified Welding Inspector
NDT Level II UT, VT, MT and PT
NACE CIP Level I Coating Inspector
AWS Certified Welding Inspector
NDT Level II UT, VT, MT and PT
NACE CIP Level I Coating Inspector
Oh it does alright, just not for long. If I had to guesstimate, the hose itself has a 10% DC @ 200A DC, and 5-10% DC @ 200A AC with balance set to -3 on that machine. Same goes for the torch. It is a 17 torch, so it's only rated at 150A at best, with a short duty cycle----how much DC? Not that much, I'd say around 30-40% @ 150A DC, even less on AC.jwright650 wrote:I wondered how that gas hose carried 200 amps of current...apparently it doesn't always...I will have to be careful wrapping all of that up when putting the welder away after I use it.
Interesting, Just had a similar issue with an AHP machine I'm demoing . Not as severe and that was running it on kill DC w/ Helium. I believe it's a cost control thing. Will be addressing possible design improvements with them. I have the Everlast 185 power tig that machine has a separate had and power hose to the torch. The power cable is significantly larger too.Oscar wrote:Don't get me wrong, the cable is very flexible, but a true super flex is even more flexible and about half the weight.
Also, this is what happens if you're not careful on AC welding:
That is the torch end. The "missing" part I had already chopped off because it was cooked from the heat in the torch that inevitably makes its way down to the fitting/cable junction during the course of AC welding where there is much more heat into the tig torch. That maroon sheath? Nowhere to be found as it had shriveled up and melted back, exposing the actual hose.
I'm guessing they were expecting the gas flow to keep the thinner gauge wire cool when welding. Obviously it doesn't (enough) get a good watercraft, CK etc torch and call it good.
Return to “Tig Welding - Tig Welding Aluminum - Tig Welding Techniques - Aluminum Tig Welding”
Jump to
- Introductions & How to Use the Forum
- ↳ Welcome!
- ↳ Member Introductions
- ↳ How to Use the Forum
- ↳ Moderator Applications
- Welding Discussion
- ↳ Metal Cutting
- ↳ Tig Welding - Tig Welding Aluminum - Tig Welding Techniques - Aluminum Tig Welding
- ↳ Mig and Flux Core - gas metal arc welding & flux cored arc welding
- ↳ Stick Welding/Arc Welding - Shielded Metal Arc Welding
- ↳ Welding Forum General Shop Talk
- ↳ Welding Certification - Stick/Arc Welding, Tig Welding, Mig Welding Certification tests - Welding Tests of all kinds
- ↳ Welding Projects - Welding project Ideas - Welding project plans
- ↳ Product Reviews
- ↳ Fuel Gas Heating
- Welding Tips & Tricks
- ↳ Video Discussion
- ↳ Wish List
- Announcements & Feedback
- ↳ Forum News
- ↳ Suggestions, Feedback and Support
- Welding Marketplace
- ↳ Welding Jobs - Industrial Welding Jobs - Pipe Welding Jobs - Tig Welding Jobs
- ↳ Classifieds - Buy, Sell, Trade Used Welding Equipment
- Welding Resources
- ↳ Tradeshows, Seminars and Events
- ↳ The Welding Library
- ↳ Education Opportunities